T400-C - la fabrication
Le plan de ce télescope est vraiment abouti et répond parfaitement au cahier des charges. Si d’aventure vous étiez tentés par cette réalisation, suivez attentivement les descriptifs énoncés. Il n’y a pas de plans cotés disponibles. Toutefois, les cotes fonctionnelles sont mentionnées dans ce site, (onglets principes et fabrication). Prenez en compte les propositions de modifications et les paragraphes intitulés « et si c’était à refaire ». Enfin, bien voir que cet instrument peut être réalisé avec des matériaux plus simples à mettre en œuvre et moins onéreux que le carbone, avec une cage secondaire en alu rivetée, comme le prototype visible sur la page « principes », et du contre-plaqué pour la base annulaire, le flex rocker et les tourillons.
La cage du secondaire
Cette partie est entièrement réalisée en composite carbone/epoxy. J’ai trouvé intéressant d’expérimenter la mise en oeuvre de ce matériau qui au final, offre des caractéristiques remarquables en termes de poids et de rigidité.
Le carbone/Epoxy
Le principe
Pour tirer une forme en matériau composite, il existe deux possibilités : soit une stratification directement dans un moule en creux (négatif), lui-même obtenu par un tirage d’un modèle (positif), soit une stratification directement sur une forme qui est conservée qu’on appelle une « âme ». Pour des raisons de facilité de mise en œuvre, je vais utiliser la deuxième méthode. La stratification consiste à faire épouser une forme avec un matériau plus ou moins souple – ici un tissu en fibre de carbone – puis de l’imprégner avec une colle – ici de la résine Epoxy – afin de fabriquer une coque rigide. Par ce procédé, nous obtenons une forme en matériau composite – ici carbone/Epoxy.
La mise en œuvre
Pour plus de détails, je vous invite à visiter des sites spécialisés comme navimodélime, site très complet sur la mise en oeuvre des matériaux composites.
La forme de base, l’âme est obtenue par un travail de menuiserie mettant en œuvre des tasseaux, des planches, des massifs de balsa. Ce matériau est choisi pour sa grande légèreté, sa facilité d’usinage et sa porosité naturelle, ce qui permet un bon accrochage de la résine. Cette forme est habillée avec le tissu de carbone préalablement découpé. Il suffit d’imprégner la fibre de carbone avec juste ce qu’il faut de résine Epoxy en tapotant avec le bout d’un pinceau. La règle veut qu’on ait le même poids de tissu et de résine. Avec ces données de base, il est facile de déterminer la quantité des produits à mettre en œuvre. Pour accélérer le processus de solidification et améliorer les caractéristiques mécaniques finales, il est judicieux d’étuver la pièce à environ 100°C.
Les matériaux
– J’ai acheté 1 kg de résine Epoxy dans la grande surface de bricolage la plus près de chez moi. Elle se dose à 45% de volume de durcisseur pour 100% de résine. L’usage de seringues graduées est une aide précieuse. Le solvant de l’Epoxy est l’alcool à brûler.
– 2 m² de toile de fibre de carbone ont été achetés à bon prix sur Ebay. C’est un tissage de 200 g/m², relativement « raide ». Les plis sont difficiles à marquer et maintenir.
– J’ai pris 3 m de ruban carbone de 50 mm de largeur unidirectionnel. Toutes les fibres sont dans la longueur, ce qui permet une reprise optimale des efforts de traction/compression.
– Enfin, je me suis procuré de la cire liquide de démoulage. Elle est appliquée copieusement au chiffon, séchée rapidement à chaud et lustrée au chiffon doux pour permettre un démoulage facile.
Le chantier
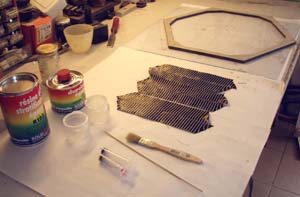
Il est important de bien préparer le chantier car le travail de la résine peut vite devenir un cauchemar. C’est sale, ça poisse, on en met partout. Mais tout rentre dans l’ordre avec un peu de méthode. Sur une feuille de papier, on voit les 2 composants de la résine, le pot pour faire le mélange, un autre avec de l’alcool à brûler pour le nettoyage, 2 seringues (repérées) pour faire un dosage précis, un bâton pour touiller, le pinceau pour l’imprégnation. Plus loin, les lés pré-découpés de tissu de carbone. Enfin, sur une vitre parfaitement propre, la forme en balsa prête à être stratifiée. On aura soin d’utiliser des gants en latex, des chiffons et un filtre respiratoire pour se protéger de ces méchantes poussières.
La découpe du tissu se fait sur un plan de travail bien dégagé et propre. Il faut bien définir l’agencement des divers éléments à assembler entre eux tout en tenant compte de l’orientation des fibres. Les lés doivent se chevaucher sur une surface généreuse et les fibres principales orientées selon les efforts à reprendre. Les formes sont tracées sur le tissu puis découpées soigneusement aux ciseaux en laissant une marge de sécurité. Elles sont stockées à plat dans l’attente de leurs mise en œuvre. Attention de ne pas effilocher les coupes (un adhésif ou un filet de colle peuvent être utiles dans ce cas) ou de déformer la trame du tissu.
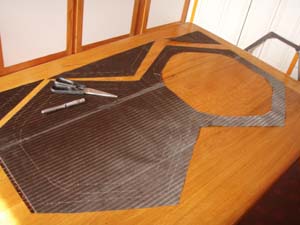
ETAPES DE FABRICATION DE L'ANNEAU
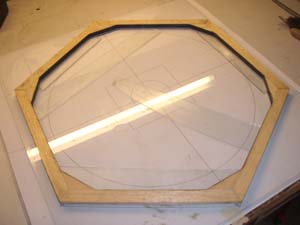
Réalisation de la forme en balsa
Après découpe et ajustage précis des différents éléments de l’âme, ceux-ci sont assemblés à la colle blanche directement sur le plan. La section des tasseaux est 10 x 20 mm. Il est important d’assurer un bon serrage des pièces entre elles et une bonne planéité de l’ensemble pendant le séchage de la colle. Une fois sec, les faces sont soigneusement poncées. L’ensemble est étonnamment léger et rigide pour une manipulation aisée. Mais pas suffisamment pour l’usage destiné. C’est pourquoi il va falloir stratifier cette forme.
Mise en place des champs
Sur cette image, le champ intérieur a été collé et arasé. Pour les travaux de stratification, je travaille sur une vitre préalablement cirée pour éviter un collage inopiné de la structure sur le plan de travail. Une bande de tissu de fibre de carbone est découpée puis déposée avec soin sur la forme en balsa préalablement encollée de résine. Le tissu est ensuite imprégné en tapotant avec le pinceau. Les angles intérieurs sont bien marqués. Après séchage complet, l’excèdent de fibre est découpé à la tronçonneuse puis la coupe est parfaitement arasée à la lime et à la cale à poncer bien à plat. On procède de même pour le champ extérieur.
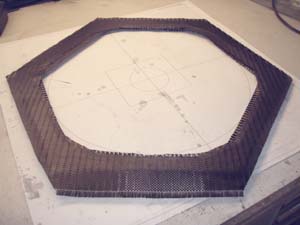
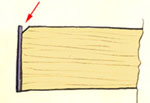
Stratification des faces
Les faces supérieures et inférieures reçoivent chacune 2 couches de tissu. La première est constituée de 6 rubans unidirectionnels, visibles sur la première image du chantier. Une fois la face sèche et bien poncée, elle est recouverte d’une pièce de tissu préalablement découpée à la forme hexagonale. Celle-ci assure une parfaite liaison des divers éléments entre eux et présente une belle finition. Pour cette étape, je n’ai pas osé mouler ces 2 faces sur une vitre pour avoir un état de surface bien lisse, craignant – à tort – des problèmes de démoulage. C’est pourquoi l’état de surface final n’est pas lisse et qu’il présente le relief du tramage du tissu, ce qui en fin de compte est assez joli.
Nota : pour traiter les angles et les renforcer, il est judicieux de faire avec un cutter un petit sillon en Vé (comme un chanfrein) entre la première face de carbone réalisée et l’âme. Cet espace se remplira de résine et de fibres lors de la stratification de la seconde face, assurant une parfaite liaison entre ces deux faces.

L’étuvage
Pour accélérer le séchage, éviter le toucher poisseux de la résine Epoxy et surtout, augmenter les caractéristiques mécaniques du composite, la pièce est mise à étuver pendant 3 heures. L’étuve est constituée d’une boîte en carton au fond de laquelle est installé un petit radiateur électrique. La pièce est suspendue par un crochet et l’étuve est fermée. La température atteint 90°C dans la partie supérieure. Le local doit être bien ventilé pour évacuer les vapeurs des solvants.
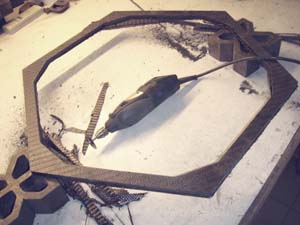
L’arasage
Une fois la résine sèche, la fibre de carbone devient très dure et rigide. Il faut découper l’excédent avec un petit disque à tronçonner monté sur une micro-perceuse. Cette phase est désagréable car très sale. Il est impératif de bien se protéger avec des lunettes et un filtre respiratoire. Pour éviter les grattouillis sur les mains et les avant-bras, il est judicieux de bien se talquer et de porter des gants en latex. La coupe est parfaitement arasée à la lime puis les arètes vives sont chanfreinées. Enfin, un ponçage soigné à l’eau permet d’obtenir une belle finition et un touché lisse exempt de bavures et d’échardes.
Nota : une autre méthode préconisée par Jacques Civetta consiste à attendre le point de prise de la résine où le matériau prend la consistance du cuir. Il est ainsi aisé de trancher l’excédent avec un cutter.
Voila, cette première pièce est terminée. Elle est superbe et ne pèse que 140 g.
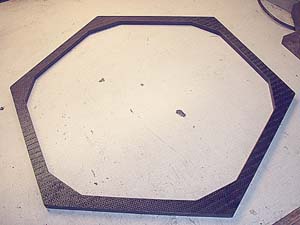
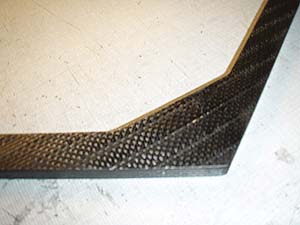
et si c’était à refaire…
Bien que je juge la solidité de cet ensemble suffisante à l’usage, la section de la cage gagnerait à être augmentée (15x20mm, voire 20x20mm), ou de mettre davantage de carbone, ou faire un profil en « L » pour une rigidité bien supérieure et un surpoids négligeable. Telle qu’elle est, elle fléchit dès lors qu’on charge le PO ou qu’on fait varier le pointage du télescope, ce qui se traduit par un petit déréglage de la collimation. C’est LE point faible de cet instrument. Ce défaut est largement compensé sur le terrain par la facilité d’emploi du système de collimation à l’oculaire et à ce jour, ça ne me gêne pas.
ETAPES DE FABRICATION DE L'ARAIGNEE
Fabrication de cornières et petits éléments
Pour l’accastillage du télescope, j’ai besoin de disposer d’éléments de base comme des cornières ou du plat en carbone. Pour ce faire, je stratifie directement une ou plusieurs couches de tissu sur un moule constitué de plaques de verre, de planches de mélaminé vissées entre elles, de plats ou de cornières d’alu. Il faut environ 5 plis de tissu de 200g pour obtenir une épaisseur d’ 1 mm. Les éléments en contact avec la résine sont préalablement cirés et lustrés pour permettre le démoulage de la pièce. Un contre-moule est aussitôt appliqué et serré fortement à l’aide de serre-joints (partie gauche de l’image). Pour obtenir précisément les épaisseurs souhaitées, il faut mettre des petites cales d’épaisseur entre les divers éléments qui constituent le moule. Après séchage, j’obtiens de belles pièces, avec des faces lisses et planes, des angles précis et bien marqués (partie droite de l’image).
Les champs rapportés sont moulés sur une seule face. Ils sont stratifiés directement sur une vitre
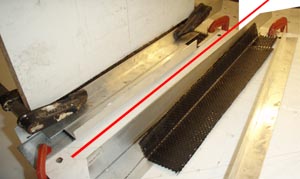
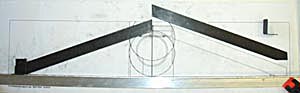
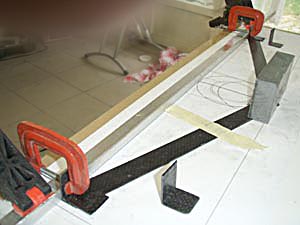
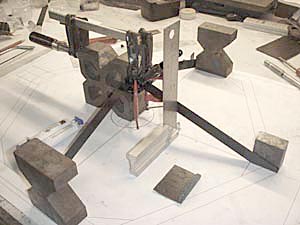
L’araignée
Cette araignée est entièrement assemblée par collage, solution plus légère, élégante et robuste que celle faisant usage de vis et d’écrous. Le collage se fait à l’Epoxy et les faces à encoller doivent être dégraissées et poncées grossièrement pour obtenir une surface rugueuse.
Les 3 branches sont débitées dans du plat de 20 x 1 mm. Leurs extrémités sont précisément ajustées aux formes et dimensions dictées par l’assemblage final.
Les 2 branches principales sont positionnées bien à plat sur le plan et collées entre elles. Cet assemblage est renforcé par une des cornières du support du miroir secondaire. A la base, 2 autres petites cornières sont collées. Elles serviront de pattes d’assemblage avec l’anneau du secondaire.
Les éléments sur support du miroir secondaire sont débités dans de la cornière et ajustés entre eux selon une disposition particulière. Ces pièces permettent et renforcent l’assemblage des branches de l’araignée.
Les parties devant présenter une épaisseur plus importante sont réalisées avec des planchettes de balsa. Toutes les faces sont recouvertes de carbone.
L’ensemble des branches est ensuite collé définitivement sur le support du miroir secondaire. C’est une opération assez délicate car il faut impérativement respecter la géométrie du tracé et cet assemblage se fait « en l’air ». L’usage de cales, de supports et de serre-joints est indispensable. L’équerrage et le positionnement des divers éléments doivent être méticuleusement vérifiés. Une fois secs, aucune latitude de réglage ne sera possible.
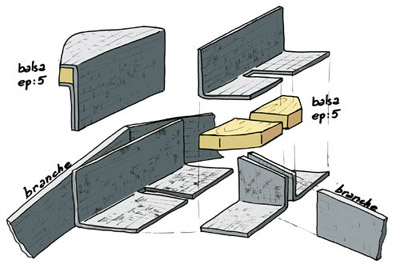
modification : à l’usage, le télescope est sensible au vent. Cela génère des vibrations rapides génantes à fort grossissement. Le point faible est l’extrême finesse de l’araignée. Je décide de la renforcer en augmentant sensiblement la section des 3 branches et en assurant un accrochage supplémentaire sur la partie interne de l’anneau de la cage. Pour ce faire, je débite et ajuste dans du plat de carbone de 1mm d’épaisseur divers éléments. L’un est mis en dessous de chacune des branches pour obtenir une largeur de 30 mm, deux autres sont collés à l’Epoxy de part et d’autre pour bien solidariser le tout et porter l’épaisseur finale à 3 mm. Deux petites équerres sont inserées dans ce sandwich pour assurer la fixation sur la face interne de l’anneau de la cage. Des échancrures sont découpées au plus juste pour permettre le passage du miroir secondaire. La rigidité de cet ensemble est alors incomparable.
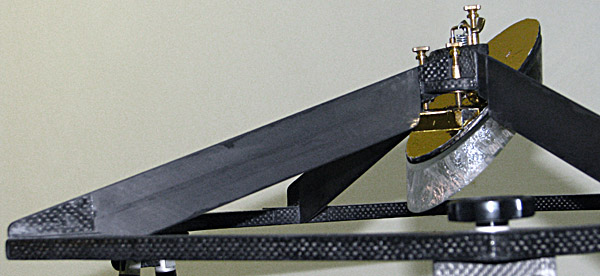
Le support du miroir secondaire
La plaque sur laquelle est collé le miroir secondaire est un sandwich carbone/balsa/carbone de 3 mm d’épaisseur. Elle est découpée aux dimensions exactes du miroir. Deux cornières stratifiées sur une âme en balsa sont positionnées et collées sur la face arrière. Elles servent de support aux 3 touches de contact avec les vis de collimation. 3 trous parfaitement repérés réalisés dans les cornières permettent un positionnement précis de ces points de contact rapportés.
Ces touches sont réalisées dans du laiton. Leur usinage permet la matérialisation du point/trait/plan dicté par le principe isostatique retenu (voir principes). Elles sont collées à l’Araldite sur les cornières. Le point est une cuvette conique réalisée avec un foret. Le trait est réalisé ultérieurement à la lime tire-point, après avoir effectué une collimation fine pour repérer exactement sa position. Le trait passe par la pointe de la vis de collimation et est orienté vers le point.
Nota : le positionnement des touches de contact doit être le plus précis possible et corrigé finement une fois l’araignée collée en place sur l’anneau du secondaire et le miroir secondaire collé sur sa plaque support. C’est indispensable pour garantir le bon centrage latéral du miroir secondaire par rapport au porte oculaire. L’araignée étant solidaire de l’anneau du secondaire, aucune latitude de réglage en ce sens n’est possible.
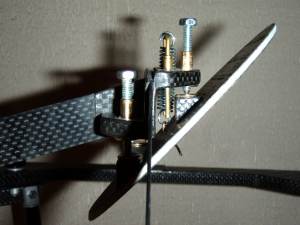
Le collage du miroir secondaire
Il est important que le miroir ne subisse aucune contrainte par rapport à la plaque support. On utilise de la colle silicone prévue pour les aquariums qui présente des caractéristiques de collage optimales et ne s’embarrasse pas d’autres considérations (fongicides, anti UV, etc.). Les surfaces à encoller sont soigneusement dégraissées à l’acétone. La plaque support, le miroir et la colle sont mis 24h dans un endroit frais pour bien égaliser leur température, et être au plus près de la température moyenne d’utilisation du télescope. En tripotant au minimum les éléments pour éviter de les échauffer, on dépose 3 ou 4 petits pâtés de colle gros comme un pois. On en profite pour déposer quelques autres pâtés de même taille sur une plaque quelconque qui serviront dans les jours suivants de témoins de prise à cœur de la colle, en les coupant au cutter. En intercalant 2 cure-dents qui font office de cale d’épaisseur, et on dépose le miroir sur sa plaque et on laisse reposer sans toucher le nombre de jours nécessaires à un parfait collage, vérifié par l’examen des « pâtés témoins ».
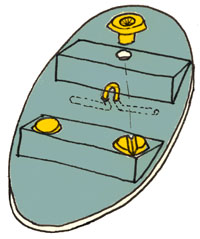
Les vis de collimation
Trois douilles filetées M4x15 dotées d’un large épaulement sont usinées en laiton. Elles sont insérées et collées sur les cornières solidaires de l’araignée. Cela permet un maintien ferme, précis et solide des vis de collimation.
L’extrémité des vis est taillée en sphère pour le contact « plan » et en cône pour les contacts «trait» et «point».
La vis matérialisant le « point » est freinée par un contre écrou une fois le réglage du miroir secondaire en hauteur effectué.
La plaque du support du miroir est fermement plaquée sur ces 3 vis par un ressort de traction suffisamment puissant, accroché par une agrafe métallique.
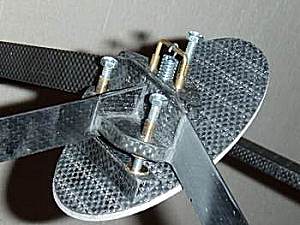
Accastillage et assemblage final
Le support du porte oculaire
Le coin de la cage hexagonale sur lequel vient se plaquer le PO est tronqué. 2 montants réalisés en sandwich carbone/balsa/carbone ép 8 mm sont ajustés et collés précisément sur la cage (image ci-contre).
En vis-à-vis des trous de fixation du PO, 4 manchons filetés sont insérés et collés dans l’épaisseur des montants les traversant de part en part. Ils servent aussi pour la fixation du passe-filtre. Le perçage des 4 trous correspondants demande du soin pour ne pas sortir de l’épaisseur des montants.
Le calage du support est vérifié avec un cheshire inséré dans le PO et une mire (équerre).
et si c’était à refaire…
Sans hésiter, j’utiliserais un porte-oculaire Feater Touch, de qualité bien supérieure au Moonlite. Ce dernier se marque et s’use avec le temps en perdant sa belle fluidité de départ.
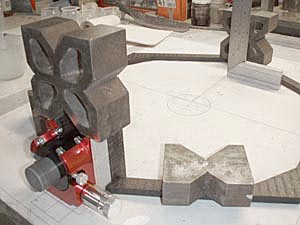
Quincaillerie
Pour assembler les divers éléments entre eux, je réalise au tour et à la fraiseuse divers types d’inserts filetés et des chapes. Ceux-ci sont réalisés en aluminium.
Les chapes sont généreusement alésées pour un gain de poids significatif. Deux gorges sont pratiquées afin d’améliorer le collage dans les tubes carbone.
Toutes ces pièces sont ensuite anodisées pour éviter les phénomènes de corrosion dus au couple carbone/alu, pour une meilleure accroche de la colle et pour obtenir une surface plus dure. Pour ce faire, les pièces préalablement dégraissées à la lessive de soude, sont suspendues dans une solution d’acide sulfurique dilué pour y subir une électrolyse, traversées par un courant de l’ordre de 1A/dm². Tout ce qui baigne doit être en aluminium (support de pièce, anode).
Une tentative de coloration en rouge a hélas, échoué. La nuance du métal n’a pas permis cette fantaisie… Imaginons un télescope tout en carbone et pièces en alu anodisées en rouge…huuuum ! Dommage.
Modification : lors des travaux de modification en 2012 pour couper les tubes en deux, j’ai trouvé un palliatif à cette question d’ordre esthétique, en teintant ces éléments avec un feutre rouge indélébile pour un résultat des plus croquignolets.
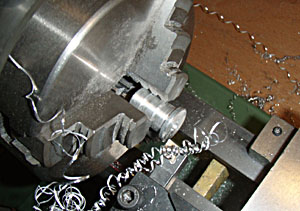
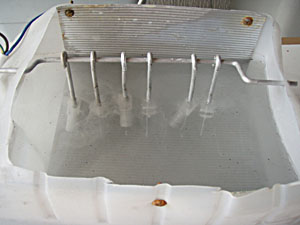
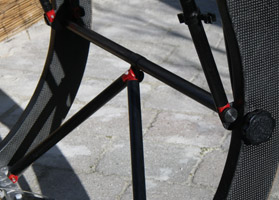
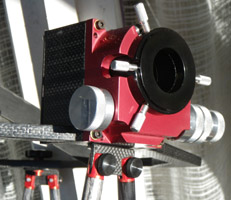
La fixation de la structure triangulée
Je me suis procuré les tubes en carbone pultrudé chez la société STRUCTIL. Ils sont réunis deux à deux sur une petite cornière par l’intérimaire de chapes en alu. Pour le montage du télescope, ces cornières sont fixées sur la cage du secondaire grâce à 3 vis à tête de serrage manœuvrables à la main.
Les 3 cornières sont réalisées en carbone/Epoxy par stratification de 14 plis de tissu pour une épaisseur finale de 3 mm. Un montage a été réalisé pour obtenir les angles idoines dictés par la structure triangulée à 6 tubes, ici 85,5° et 90°.
Des inserts filetés sont collés dans des perçages effectués sur ces cornières et en vis-à-vis sur la cage du secondaire. Après avoir fait sauter quelques filets sur les vis et les inserts, les vis de serrage deviennent «imperdables» : elles peuvent tourner librement mais restent solidaires de la cage du secondaire.
Les chapes ne doivent présenter aucun jeu une fois assemblées sur les équerres. Les cotes d’usinage sont réalisées pour permettre un montage légèrement serré.
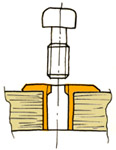
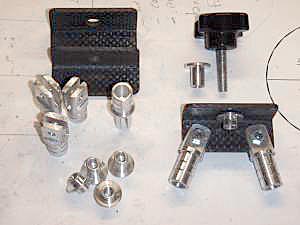
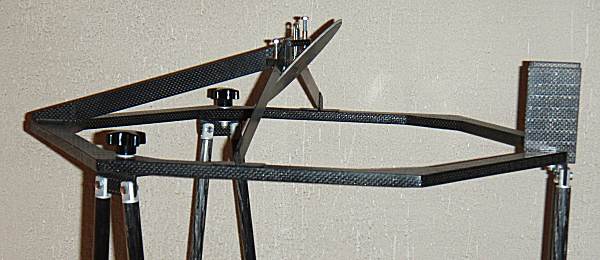
Le barillet
Etapes de fabrication
Le cadre
Il est réalisé en tube carré d’aluminium de 20 x 20 x 1,5 mm, assemblé par des goussets en tôle d’alu ep 1, rivetés et collés à l’Araldite. La qualité de la géométrie finale dépend de la précision des coupes et du respect des angles d’assemblage. Il est utile de se faire des petits montages d’usinage à cet effet. L’emploi de rivets « pop » à tête large donne, outre une meilleure qualité à l’assemblage, un aspect qui me plaît bien. Le résultat est d’une robustesse remarquable.
C’est un principe de construction très simple à mettre en œuvre pour un rendu de qualité.
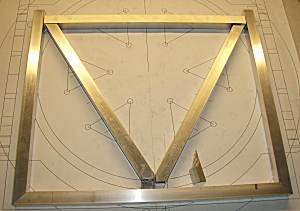
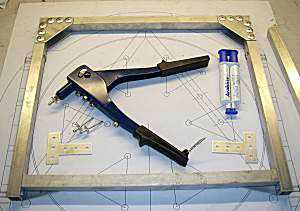
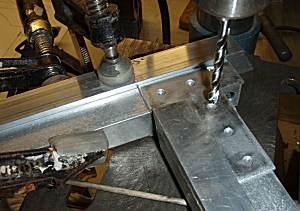
Les 2 leviers de collimation
Les 2 leviers peuvent se mouvoir indépendamment l’un de l’autre pour permettre la collimation. Ils sont articulés sur la traverse basse du cadre et dessinent avec celle-ci un triangle équilatéral. Réalisés en tube carré de 20 x 20, leurs extrémités sont usinées pour remplir une fonction particulière. D’un côté, nous avons l’articulation proprement dite faite d’un axe en laiton de 2 mm de diamètre, parallèle et articulé à la traverse basse. De l’autre côté, un profilé en T est encastré/collé pour permettre d’une part, le réglage en hauteur pour la collimation et d’autre part, le guidage latéral des leviers pour assurer un parfait maintien de ces parties mobiles. (voir aussi schéma en bas de cette page).
Les axes – comme tous les autres dans cette réalisation – sont simplement arrêtés en coudant leurs extrémités à la pince, ce qui simplifie considérablement le travail.
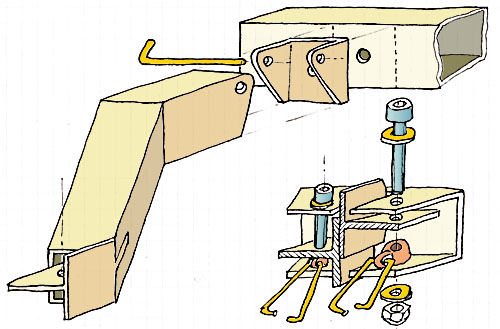
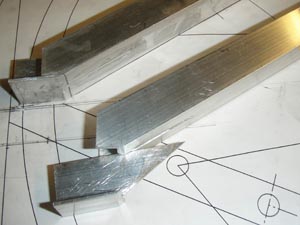
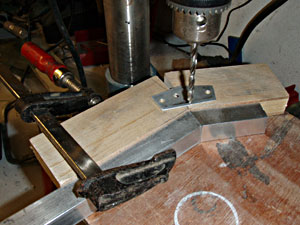
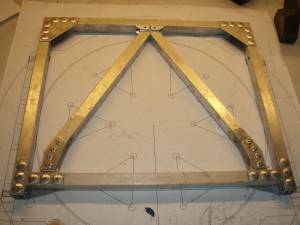
Le support à 18 points du miroir
Le principe du barillet à 18 point flottant est énoncé dans la page « principes ». Il est primordial de comprendre qu’un barillet est une balance de précision complexe. Le moindre point dur, la moindre résistance se traduira par un déséquilibre notoire du système et génèrera des contraintes dans le miroir primaire qui effondreront ses performances .
Les 3 leviers intermédiaires (à ne pas confondre avec les 2 leviers de collimation décrits au chapitre précédent) sont réalisés à partir d’un U en alu de 25 x 25 x 2 mm. Ils sont articulés en leur milieu par un axe de dia 2 mm. Ce profil en U permet de recouvrir les éléments du cadre du barillet et fait gagner en compacité comme on peut le constater sur la photo ci-contre.
L’un des leviers n’a pas de réglage en hauteur. Il est articulé directement sur la traverse basse du barillet. Les deux autres le sont chacun sur un levier de collimation, réglables indépendant l’un de l’autre.
Les triangles de flottaison sont réalisés en sandwich 2 plis carbone 600-200 gr/balsa 2 mm/carbone 600 -200 gr (image ci-dessous à gauche). La liaison entre ces triangles et les leviers se fait par des chapes à rotule, utilisées en modélisme. Ces chapes se composent d’une partie en nylon noir, ici livrées en grappe (image ci-dessous du milieu, en haut). Je les sépare à la pince coupante puis j’arase la « queue » inutile ici. J’obtiens au final des petites bagues en nylon (image ci-dessous du milieu, en bas à droite). La rotule est une bille d’acier percée d’un trou dia 3 mm. Cette bille est insérée à force dans la bague (image ci-dessous à droite, en bas à droite). Elle peut bouger librement en tout sens sans effort mais aussi sans jeu ce qui est le but recherché.
Les triangles sont percés et lamés pour recevoir les chapes à rotule (image ci-dessous à droite, en haut à droite). Les chapes y sont insérées et collées à l’Araldite (image ci-dessous à droite, à gauche). Une fois secs, les triangles sont fixés sur les leviers, grâce à des petites vis M3 qui passent à travers la rotule, le levier et un écrou frein M3. Au droit de ces écrous, les leviers de collimation et la traverse basse du cadre sont percés pour permettre le passage de ces écrous sans entraver le mouvement des leviers (voir schéma ci-contre).
Au final, j’obtiens un barillet d’une précision redoutable, sans aucun jeu et d’une sensibilité extrême, chaque élément entrant en mouvement à la moindre sollicitation, au moindre souffle de vent !
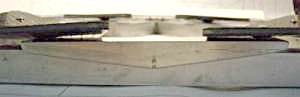
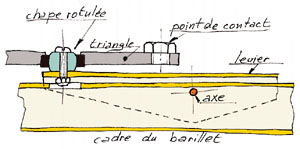
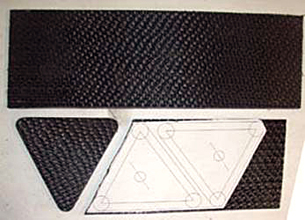
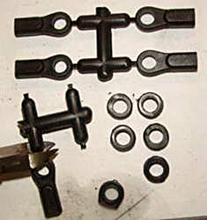
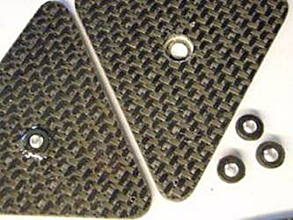
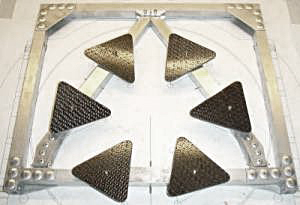
Les tourillons
Etapes de fabrication
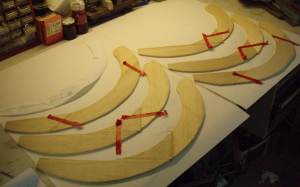
Réalisation de la forme en balsa
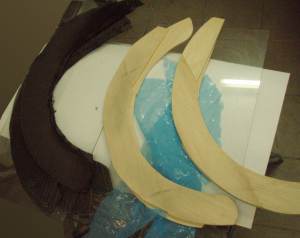
Préparation des divers éléments
Je vais stratifier les 2 tourillons ensemble, en une seule étape. Pour ce faire, chaque pli de carbone est préalablement découpé à l’aide d’un gabarit. Ils sont stockés bien à plat sur le plan de travail, dans l’ordre d’utilisation. Au total, il y a 6 plis de tissu de carbone par tourillon.
Les éléments de balsa sont finement poncés sur leurs faces.
Je vais tester un film de démoulage. Il est découpé aux dimensions idoines.
Enfin, comme toujours, j’utilise une vitre comme plan de travail.
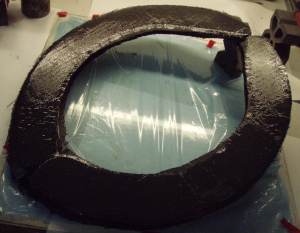
La stratification
Sur la vitre, j’applique le film de démoulage et le tends avec quelques bouts de ruban adhésif à la périphérie.
Pour une meilleure qualité d’imprégnation (nous sommes fin décembre…), je tiédis la résine Epoxy à 35 °C environ. Elle est ainsi plus fluide mais sa prise s’en trouve un peu accélérée. Il faut travailler vite et bien. J’en prépare de petites quantités à chaque fois (30 cm3) ce qui me permet de traiter environ 2 imprégnations.
Chaque pli est imprégné directement en place. Chaque face des planches en balsa est pré-imprégnée juste avant d’être posée ou de recevoir son pli de tissu. Pour assurer une bonne cohésion entre le bois et le tissu, je maroufle en frappant avec un maillet.
Enfin, le dernier pli est recouvert d’un film de démoulage puis une vitre est déposée sur le tout et pressée par des poids.
Je place l’ensemble dans l’étuve pour quelques heures de durcissage. C’est avec un grand plaisir que je démoule sans difficulté ces 2 blocs. Seul petit bémol, j’ai mal utilisé le film et de petits plis apparaissent. Je les ferais disparaître au ponçage.
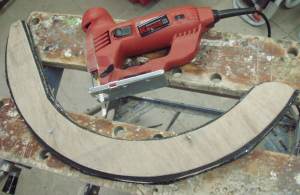
La découpe
Les tourillons étant constitués d’un empilage de 10 éléments distincts, ceux-ci sont découpés plus largement que prévu. Après la stratification, j’obtiens donc 2 ébauches de tourillons. Pour obtenir la forme finale, j’utilise un gabarit en CTP découpé très précisément aux bonnes dimensions. 3 trous parfaitement repérés permettent un positionnement parfait du gabarit sur les ébauches en carbone/balsa. Ces trous seront utilisés ultérieurement pour la fixation des tourillons sur le barillet et de l’entretoise en partie haute.
Les formes sont obtenues à la scie électrique, puis à la lime et enfin au ponçage.
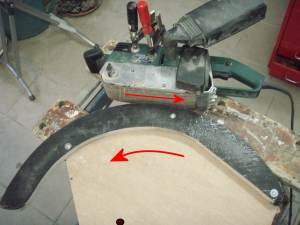
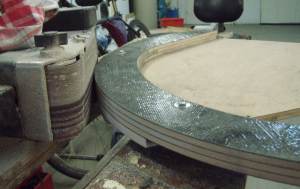
La dressage de la face de frottement
Pour avoir de bons mouvements avec le télescope, il est indispensable que les faces de frottement des tourillons soient bien circulaires, bien planes et d’équerre, que leur centre, correspondant à la position du centre de gravité du télescope, soit parfaitement positionné.
Pour ce faire, j’ai réalisé un montage en CTP de 10 mm. Une planche est directement vissée sur le plateau fixe d’un établi réglable. Un axe en acier y est solidement implanté. Une deuxième planche et posée dessus et peut pivoter librement autour de cet axe. 3 inserts filetés sont précisément positionnés sur cette planche par rapport à l’axe de rotation. Ils correspondent aux 3 trous de référence des tourillons. Ceux-ci peuvent être installés et fixés solidement sur ce montage.
Une ponceuse à bande est fermement bridée sur le plateau mobile de l’établi. L’équerrage de la semelle est finement ajusté par rapport au montage.
Il suffit maintenant de régler la profondeur d’usinage en agissant sur le plateau mobile de l’établi, puis, une fois la ponceuse mise ne marche, de faire tourner doucement le tourillon sur son montage.
ATTENTION : le travail doit toujours se faire « en opposition », sous peine de dégâts. C’est à dire que les forces d’usinage doivent s’opposer aux forces d’avance.
Au final, j’obtiens 2 magnifiques tourillons, avec une géométrie parfaitement respectée. La rigidité est absolument incroyable et le poids de ces 2 éléments réunis n’est que de 510 gr !!!
On voit ici la composition du sandwich.
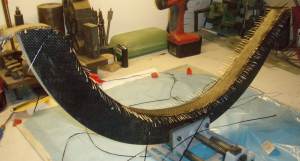
Stratification des champs
Cette étape a été plus ardue à réaliser que ce que j’imaginais. En effet, les formes concaves sont délicates à bien stratifier notamment avec le tissu unidirectionnel lourd, à bien faire adhérer sur les flancs. L’arrondi en bout des tourillons avait tendance à faire décoller les plis. Enfin, la découpe, la manipulation et la mise en œuvre des bandes étroites de tissu de carbone est assez problématique, les bords ayant la fâcheuse tendance à s’effilocher. Moralité, j’aurais dû tailler ces bandes bien plus larges et, comme je l’ai fait par la suite, traiter les bords avec un filet de colle cyanoacrylate.
Les champs sont constitués de 1 pli 200 gr tissé, 1 pli 450 gr unidirectionnel et 1 pli 200 gr tissé.
Les divers champs (face concave, extrémité et face convexe) sont stratifiés les uns après les autres, après avoir arasé et poncé le surplus de tissu à chaque fois.
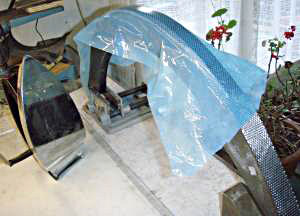
La bande de frottement
Suite aux difficultés rencontrées lors de la précédente étape, j’ai découvert et utilisé ici les propriétés étonnantes du tissu de carbone « poudré ». Celui-ci est faiblement pré-imprégné de résine thermodurcissable. Il est alors possible de le travailler à chaud pour le mettre en forme et/ou le faire adhérer sur une surface.
Pour garantir une bonne géométrie de ces surfaces, je n’ai utilisé qu’un seul pli de tissu unidirectionnel de 450 gr poudré. Il est mis en oeuvre à l’aide d’un fer à repasser sous lequel est interposé un film de démoulage. Il est ensuite imprégné de résine. Pour une meilleure qualité d’imprégnation, l’Epoxy est utilisée chaude. Le résultat est parfait.
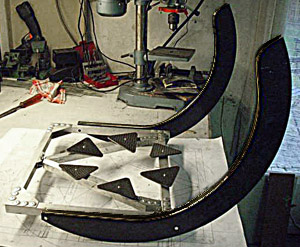
Les finitions
Une fois les champs arasés, l’ensemble est soigneusement poncé à l’eau pour obtenir une coquette finition. Les inserts filetés seront collés ultérieurement. J’obtiens en final 2 belles pièces de 530 gr au total d’une étonnante rigidité.
La base annulaire
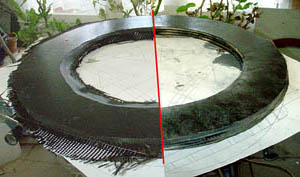
Fabrication
Cet élément est réalisé selon le même procédé que celui utilisé pour les tourillons (cf ci-dessus). Pour obtenir l’épaisseur finale de 25 mm, le sandwich est composé de 2 plis carbone tissé 200 gr, 1 planche balsa 8 mm, 1 pli carbone 200 gr, 1 planche balsa 8 mm, 1 pli carbone 200 gr, 1 planche balsa 8 mm, 2 plis carbone 200 gr.
Pour avoir un meilleur état de surface, je tends le film de démoulage avec du ruban adhésif.
Sur la partie gauche de la photo, la base brute de démoulage après étuvage, sur la partie droite, la base après arasage au disque à tronçonner monté sur micro-perceuse.
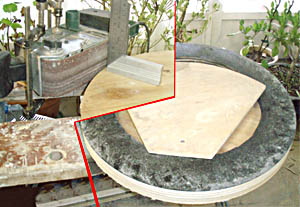
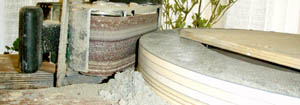
Le dressage de la face externe
C’est sur cette partie que se fera le guidage en rotation du flex-rocker. Par conséquent, la géométrie cylindrique doit être respectée. La réalisation d’un montage s’impose.
L’anneau est bridé sur un plateau circulaire. Un axe central permet à l’ensemble de tourner face à une ponceuse à bande solidement fixée sur le plateau mobile de l’établi (partie droite de l’image).
Au préalable, l’équerrage de la ponceuse est soigneusement contrôlé (partie gauche de l’image).
Remarquez la structure du sandwich carbone/balsa, visible sur la face externe en cours d’usinage.
ATTENTION : comme déjà dit, le travail doit se faire «en opposition», sous peine de dégâts…
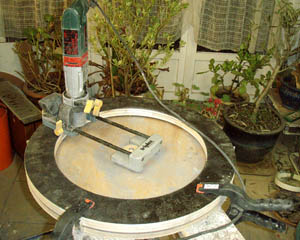
Le dressage de la face interne
Pour cette opération, l’anneau est fixé sur l’établi. Une perceuse est fixée sur un montage de type « défonceuse ». Elle est équipée d’une fraise cylindrique. Le guide latéral est utilisé comme une verge et permet à l’ensemble de pivoter autour de l’axe central.
Il ne reste plus qu’à stratifier les champs.
Cette pièce présente une rigidité absolument étonnante.
Le flex-rocker
Fabrication
Cet élément est particulièrement fin et léger. Il est constitué d’un sandwich minimaliste de 2 plis carbone 200 g, 1 planche balsa 2 mm, 2 plis carbone 200 g. Dans un premier temps, les planchettes de balsa sont assemblées sur champ par collage (image ci-contre).
La forme est ensuite découpée au cutter puis stratifiée selon les étapes illustrées sur l’image ci-dessous à gauche. Partie gauche, le pli de tissu est déposé sur le film de démoulage puis enduit de résine. Le sandwich est ensuite monté puis mis sous presse avec une vitre et des poids. Partie du milieu, le sandwich est démoulé, l’excédent de tissu arasé à la tronçonneuse. Partie droite, la forme définitive est obtenue à la lime (image ci-dessous).
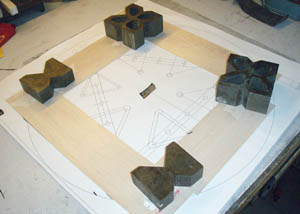
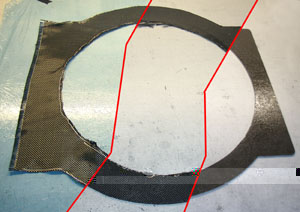
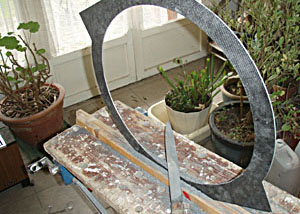
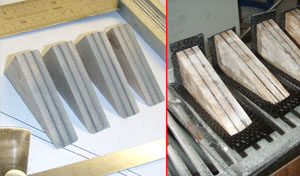
Les cales
Les 4 cales qui supportent les patins de téflon en contact avec les tourillons sont réalisés en sandwich de même composition que ces derniers, pour une épaisseur identique. Sur la partie gauche, les 4 cales découpées aux dimensions exactes. A droite, la stratification des champs en cours de séchage, sur une vitre posée sur un radiateur.
Elles sont collées à l’Araldite sur le flex-rocker. Leur positionnement doit être soigné car il détermine un fonctionnement correct du mouvement d’altitude.
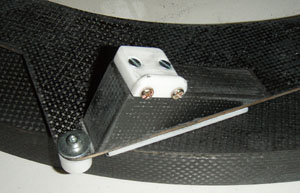
Les patins de frottement
Les patins sont en Téflon et frottent directement sur les surfaces en carbone soigneusement poncées. Ils sont débités à partir d’une barre de 22x25mm, les faces sont dressées et poncées au 600.
Pour les tourillons d’altitude, ils sont en deux parties assemblées par vis pour réaliser le frottement lui-même et le guidage latéral.
Pour le frottement sur la base annulaire, 4 patins reprennent les dimensions des embases des cales et sont placés sous celles-ci pour en assurer une parfaite stabilité.
Enfin, le guidage en rotation est assuré par 4 pions vissés dans les angles du flex-rocker venant frotter sur la face externe de la base annulaire.
Tous ces éléments sont vissés dans le flex-rocker par l’intermédiaire d’inserts filetés en laiton collés à l’Araldite.
modification 1 : à l’usage, le guidage en rotation n’apporte pas satisfaction. Les 4 pions auraient dus être implantés sur une base carrée. Elle est ici trop rectangulaire et engendre un effet de coincement du rocker.
Le guidage se fait maintenant par l’intérieur de la base annulaire. 4 roulements à billes équidistants assurent ce guidage. Ils sont vissés sur des pattes ajoutées à l’intérieur du flex-rocker.
et si c’était à refaire…
Comme dit ci-dessus, je ferais une embase carrée, afin d’implanter les patins de guidage latéral à 90° les uns des autres.
modification 2 : lors des premiers essais, je ne suis que modérément satisfait de la qualité de frottement des patins directement au contact sur le carbone entre la base annulaire et le flex-rocker. Les poussières ou le sable du désert qui s’y déposent rendent rapidement les mouvements durs. De plus, lors d’une sortie d’hiver, j’ai remarqué un phénomène de collage généré par le froid. J’ai profité d’une proposition de l’ami Denis, qui gracieusement m’a offert des chutes d’Ebony Star que j’ai collé à la Néoprène sur les surfaces de frottement de la base annulaire et des tourillons. Avec ces deux modifications, j’obtiens une excellente qualité de mouvement sur les deux axes.
Assemblage final
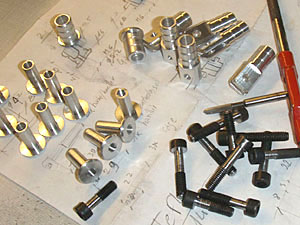
La quincaillerie
Comme pour la partie haute, des pièces en alu, chapes, inserts et embouts filetés, sont réalisées au tour puis sont anodisées.
La visserie est modifiée pour la rendre « imperdable ». Les vis sont équipées d’une tête en plastique pour les rendre manœuvrables à la main. En tout, 10 vis suffisent pour l’assemblage final du télescope : 6 pour la structure triangulée en partie haute et basse, 4 pour les tourillons.
Toujours dans un souci de gagner du poids, les 12 vis qui relient les chapes aux équerres ont été changées par d’autres en nylon. Une tête de vis moletée permet de les serrer manuellement.
Enfin, des équerres en carbone ep 3 mm sont stratifiées, découpées et poncées. Elles servent pour la fixation de la structure triangulée sur les parties haute et basse du télescope.
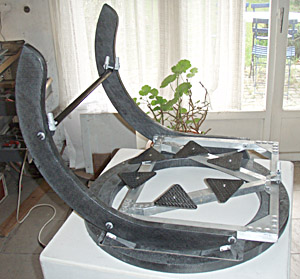
La partie basse
Les divers inserts filetés sont collés en place sur le barillet et les tourillons.
L’entretoise reçoit ses embouts filetés.
Ce n’est pas sans une certaine émotion que pour la première fois, j’assemble la partie basse du télescope.
1er assemblage à blanc
Puis, ayant refait 2 équerres d’assemblage légèrement défectueuses et taillé les tubes avec une longueur un peu plus généreuse que nécessaire, je procède au premier assemblage à blanc du télescope.
Je peux enfin voir et apprécier à loisir l’aspect global de l’instrument. Je suis comblé !
J’apprécie son élégance mais aussi certains détails pratiques. Je remarque particulièrement la parfaite hauteur du porte-oculaire, sa position ainsi que l’absence de porte-à-faux. La triangulation basse bien évasée permet outre un renforcement de la structure, une installation aisée du miroir sur le barillet.
En l’état, l’ensemble de la structure pèse 3kg760.
modification : les contraintes liées à la sécurité aérienne sont de plus en plus draconiennes et pénibles. Ce qui était possible hier ne l’est plus aujourd’hui et lors d’un séjour aux Canaries en 2011, j’ai eu les plus grandes difficultés à faire passer le matériel. Désormais, un seul bagage en soute est admis par passager. L’étui à tube que je faisais régulièrement et facilement passer en bagage cabine n’est plus toléré. Il doit alors passer en bagage en soute et compte comme un bagage supplémentaire, ce qui fait l’objet d’un surcoût. De plus même en soute, ses dimensions en font un objet facilement perdable sur les tapis roulants des aérogares. Aussi, j’ai décidé de tronçonner les tubes en 2 pour les loger dans mon sac de voyage et résoudre de façon définitive ce problème aujourd’hui sujet à caution.
Tronçonner ces beaux tubes en carbone pultrudé n’a pas été une décision facile. J’ai beaucoup réfléchi à un système de raccord efficace, simple, robuste et léger. J’ai retenu une solution faisant appel à un manchon pour assurer la rigidité de l’ensemble, réalisé dans un tube en carbone, usiné à 11,5x9x8o mm. L’assemblage est bloqué par un écrou et une partie filetée, éléments récupérés sur un presse étoupe en nylon pour câble dia 14mm, adapté pour la circonstance. La partie filetée est collée à l’extrémité d’un tronçon. Une petite bague débitée dans un tube en alu et collée sur l’autre tronçon permet de matérialiser un collet sur lequel vient s’épauler l’écrou, tout en pouvant tourner librement. La perpendicularité des coupes doit être de qualité. C’est pourquoi j’ai dressé ces faces sur un tour.
La structure n’est séparée en deux que pour les nécessités du voyage aérien. En utilisation courante, elle reste entière et est stockée dans l’étui d’origine.
et si c’était à refaire…
Bien que ne pensant pas que ce soit un point faible pénalisant, je passerais par sérénité le diamètre des tubes en 16×1,5mm, toujours pour un surpoids négligeable.
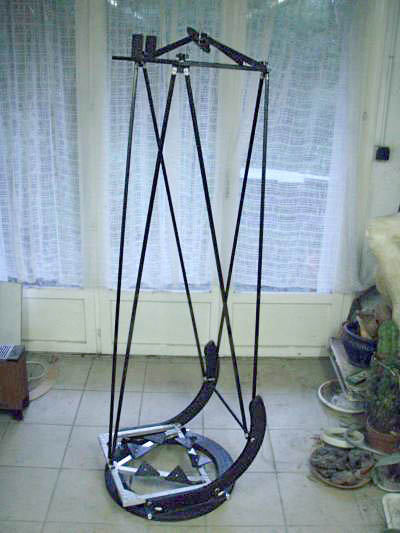
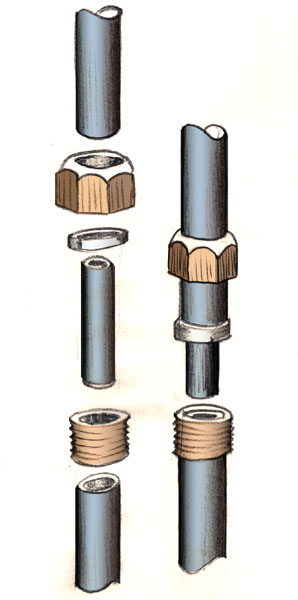
Les travaux de finitions
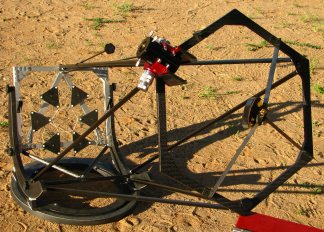
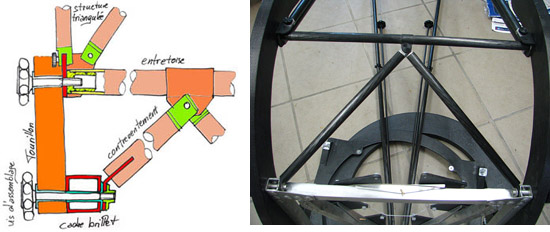
Le contreventement
Afin d’assurer une parfaite rigidité latérale de la partie basse du télescope, je mets en place une triangulation en tube carbone de 16 mm qui assure le contreventement du télescope (photo ci-dessus). Deux barres sont articulées au centre de l’entretoise par des demi-chapes. Cet ensemble se plie et les éléments restent solidaires lors du démontage. Un insert fileté est collé à chaque extrémité de ce montage. L’assemblage se fait par les vis de manœuvre manuelle de montage du télescope. Une paire assure la liaison entre les tourillons, le cadre du barillet et les barres de contreventement, l’autre paire liaisonne les tourillons, les équerres d’assemblage de la structure triangulée en partie basse et l’entretoise, comme on peut l’appréhender sur le schéma ci-dessus.
C’est du béton !
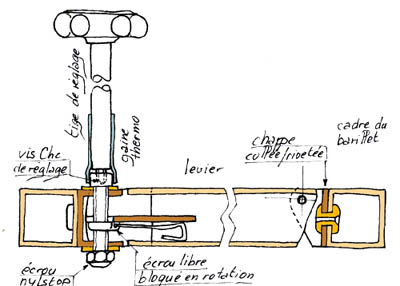

Le système de collimation avant
Comme dit plus haut, la collimation du miroir primaire se fait en agissant sur 2 leviers. Pour ce faire, un système vis/écrou passe par l’extrémité de ces leviers. Sur la tête de vis ChC vient s’emboîter une tige de manoeuvre en tube carbone de 6 mm équipée à une extrémité d’un tronçon de clé Allen (partie droite de la photo) et de l’autre d’un large bouton moleté (partie gauche de la photo). Les tiges sont maintenues par 2 clips en plastique fixés sur la structure triangulée (accessoire de moto qui permet la fixation des diverses câbleries) . Ainsi, on peut collimater finement l’instrument l’oeil à l’oculaire avec un confort inégalé. C’est du pur bonheur !
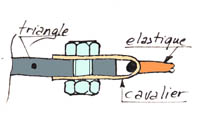
Les points de contact du barillet avec le dos du miroir primaire
Ces points sont matérialisés par des têtes de vis en nylon HM6. Elles offrent un excellent contact avec le dos du miroir. Elles sont vissées dans les triangles de flottaison. Pour tenir les triangles dans la bonne configuration, leurs sommets pointant vers le centre sont réunis par un anneau héxagonal évidé découpé dans une feuille en plastique.
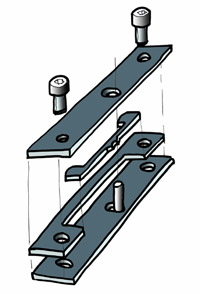
Le chercheur
Un chercheur de type Quickpoint avec variateur d’intensité est monté sur une queue d’aronde, collée sur une petite équerre en carbone sur la cage du secondaire. L’instrument étant démontable, il est important d’avoir un système de collimation aisément manoeuvrable à la main grâce à des vis à tête moletée.
Le passe-filtres
Deux glissières en carbone sont vissées à l’arrière de la console qui supporte le porte-oculaire. Réalisées par empilage de 3 plats de carbone de 1 mm d’épaisseur, l’une est équipée d’un ressort taillé à même la plaque intermédiaire pour assurer via un pion, le crantage de la plaque porte filtre.
Ainsi, deux filtres sont toujours à demeure, un OIII Lumicon, un UHC-S Baader et aujourd’hui un H-beta. Le trou resté libre participe au bafflage des entrées parasites de lumière sur l’oculaire.
Le baffle
Il est primordial qu’aucune lumière parasite ne vienne toucher la lentille d’entrée des oculaires. Il est facile de visualiser cela : il suffit de mettre en place dans le PO l’oculaire le plus sensible à ce phénomène, celui qui présente le plus grand champ. En prenant un peu de recul et en plein jour, on observe finement la pupille de sortie. Avec attention, on remarque que c’est l’image inversée de l’intérieur de la cage secondaire. On analysera la forme que doit avoir le baffle, mais aussi de tous les éléments trop clairs ou brillants qui sont visibles : vis, tranche du miroir secondaire, quincaillerie, etc… Tous ces éléments devront être masqués ou noircis.
Le baffle est découpé dans une chemise en plastique. Il se fixe par 3 élastiques sur la cage du secondaire.
Le support du PO et le passe-filtre participent au bafflage.
L'isolation du miroir secondaire
L’isolation de la plaque support du secondaire est réalisée avec de la couverture de survie. Elle est découpée à la bonne forme et est collée au scotch double-face sur le carbone.
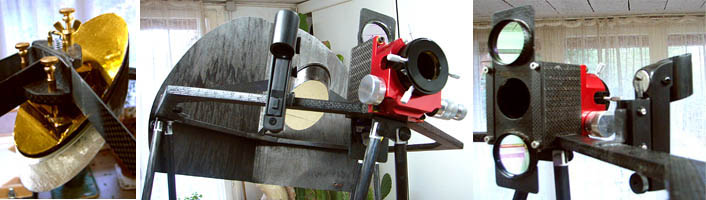
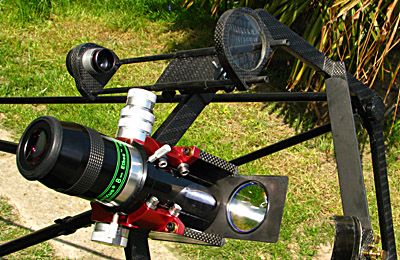
Un nouveau chercheur
J’éprouve parfois le besoin d’avoir un bon chercheur optique. J’en ai réalisé un qui peut se mettre à la place du Quickpoint au besoin. Réalisé à partir d’optiques de jumelles 7 x 50, le chercheur est de forme totalement épurée et entièrement réalisé en carbone. Deux platines en sandwich carbone/mousse 10mm supportent l’une l’objectif, l’autre l’oculaire. Elles sont reliées par 2 tubes dia 6mm. La platine de l’objectif peut coulisser afin de permettre la mise au point. cet ensemble coulisse sur une platine qui permet la collimation de la visée et la fixation sur la petite queue d’aronde, en reprenant le même concept que celui du Quickpoint. Cette partie est un assemblage de plaques en sandwich carbone/balsa 2mm. Tous les trous et les taraudages sont repris par des inserts en tôle d’alu. L’ensemble pèse 160g.
Désormais, je n’utilise que ce chercheur, fustigeant définitivement les modèles à piles qui prennent un malin plaisir à vous lâcher quand vous êtes au bout du monde.
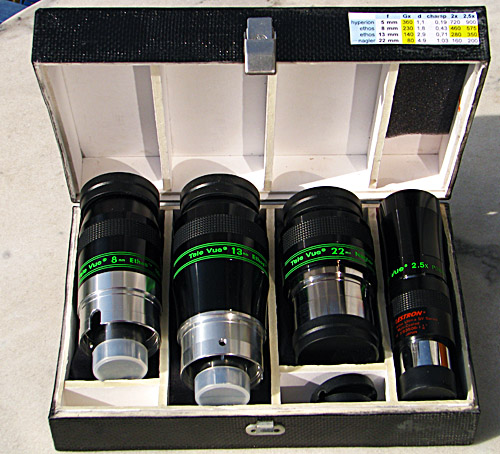
Les oculaires
La garde robe de ce magnifique télescope est constituée d’un Nagler 22mm, d’Ethos 13 et 8mm, d’une barlow Celestron Ultima 2x et d’une Powermat 2,5x. Cela permet un étagement de grossissements idéal de 80x, 140x, 230x, 280x, 350x, 460x et 575x, véritable vitesse de croisière de l’instrument. Toutefois, l’acquisition d’un 5 mm permettrait des grossissements encore plus importants avec 720x et 900x, le miroir primaire le permettant aisément.
Ces accessoires sont rangés dans une valisette sur mesure en carton plume dont les faces externes sont stratifiées avec du carbone.
J’ai craqué pour l’acquisition d’un Ethos 6mm afin de compléter la gamme et de disposer d’un étagement davantage optimisé : 80x, 140x, 230x, (280x), 300x, (350x), 460x, (575x), 600x et 750x. Une nouvelle valisette est donc de circonstance.
Après avoir testé le fantastique Ethos 21mm sur ce télescope, ce sera peut-être la folie suivante que je m’offrirais en remplacement du Nagler 22mm, bien que le joujou nécessite un contrepoids pour contrecarrer le déséquilibre notoire engendré. Mais plus sagement, j’ai complété la gamme par un Nagler 26mm, mieux corrigé en coma que le 22mm. Au regard de sa taille, il ne fait pas partie de la panoplie « voyage en avion » et reste dans sa boîte d’origine.
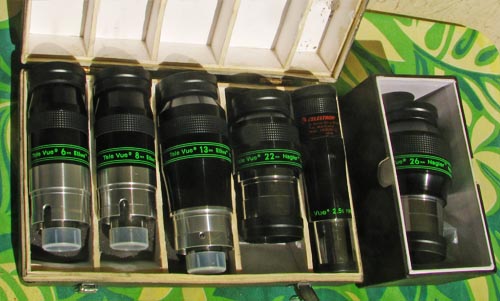
Les boites de transport
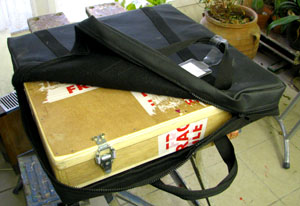
La valise du miroir primaire
Cette valise en CTP est volontairement solide. Bien que je l’utilise en bagage cabine lors des transports aériens, je suis obligé de considérer que ce bagage peut être refusé et envoyé en soute. Pour le rendre discret, je lui ai fait un sac de transport en Skaï noir qui de plus, le protège de la poussière et des intempéries. Le miroir demandant à être manipulé à chaque utilisation, j’y entrepose des gants de coton afin d’éviter toutes traces de doigts sur la surface optique.
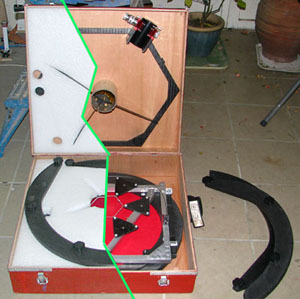
La valise du télescope
J’avais prévu au départ de faire cette valise en carbone. Mais il est des décisions sages à prendre sous peine d’éterniser inutilement un chantier. Je me suis rabattu sur une solide boîte en CTP de 8 mm, ne voulant courir aucun risque lors des transports aériens. Un CTP de 5 mm aurait pu suffire (comme avec le T400 du club) mais j’ai joué ici la sécurité. La caisse est exactement dimensionnée aux divers éléments du télescope, une fois judicieusement empilés entre eux. La cage secondaire est vissée dans le couvercle. Des cales en mousse extrudée calent fermement l’ensemble et un tube en carton bakélisé fait office de colonne de renfort central et d’étui de protection du miroir secondaire.
L'étui à tubes
Cet étui abrite la structure triangulée, l’entretoise triangulée et les 2 tiges de collimation. Il est réalisé en Skaï noir, équipé de sangles de fermeture et de transport.
Le bilan
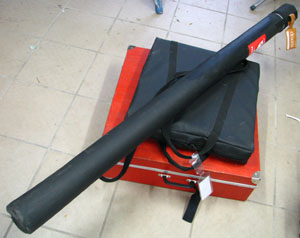
Télescope seul | Télescope en colis | |
miroir | 10,3 kg | 45 x 45 x 8 cm 14,2 kg |
télescope | 4,0 kg | 58 x 58 x 17 cm 9,6 kg |
tubes | 0,970 kg | 150 x 8 cm 1,2 kg |
total : | 15,3 kg | 25 kg |
Comme on le constate, le télescope pèse un peu plus de 15 kg, ce qui était l’objectif de départ. Ce pari est donc gagné et, s’il n’est peut-être pas le plus léger de sa catégorie, il doit certainement être dans le peloton de tête des T400 ultra-légers. Qui relève le défi de faire moins ? C’est chose possible en prenant un miroir allégé.
Par contre, pour des raisons évidentes de protection, dictées par les contraintes des transports aériens, je lui ai fait de solides conteneurs. Mais on remarque que ceux-ci ne sont pas ultra-légers !
Toutefois, je me retrouve au final avec un superbe engin remarquablement transportable et cela en toute sécurité. Là aussi, le pari est tenu. Ce système a fait ses preuves lors de son inauguration en 2008 au Sahara. Des vols internationaux aux vols intérieurs, après 3 tempêtes de sable et jusqu’aux pistes défoncées parcourues en 4×4, le télescope a toujours été parfaitement protégé.
A ce jour, il est toujours en parfait état bien qu’ayant à son actif bien des périples, parfois en rudes conditions (Namibie, Canaries, Hawaï, Chili, Australie, etc.)
Une table équatoriale
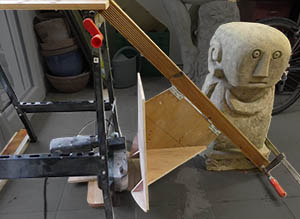
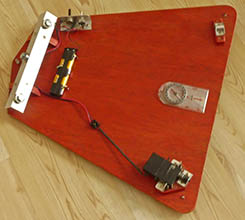
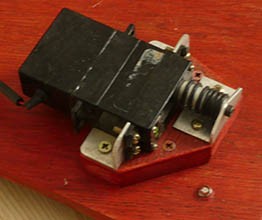
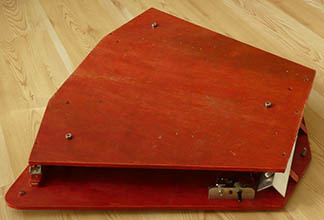
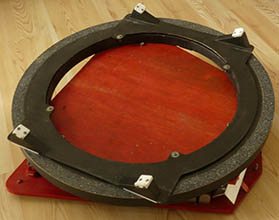
Une chaise d'observation
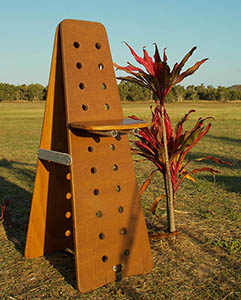
Pour les voyages lointains, je me contente d’un tripode pliant assez haut sur patte, léger et compact. Mais pour les circonstances où poids et encombrement ne sont pas une contrainte, j’éprouve le besoin d’avoir une chaise réglable en hauteur, et cela du sol jusqu’à la position où l’on est quasi debout – très fatigante à tenir. Elle est réalisée avec 2 planches en contreplaqué respectivement de 18 et 12mm d’épaisseur, de 1 mètre de long, 35cm à la base et 20cm en partie haute où elles sont articulées par 2 charnières. L’écartement est maintenu par une sangle en partie basse et un compas de verrouillage. Sous la planche d’assise sont rivetés 2 tubes en aluminium dont l’extrémité à été travaillée en forme d’obus pour faciliter l’insertion dans les alésages. Un concept très pratique à l’usage et relativement peu encombrant une fois plié.