Une planchette équatoriale
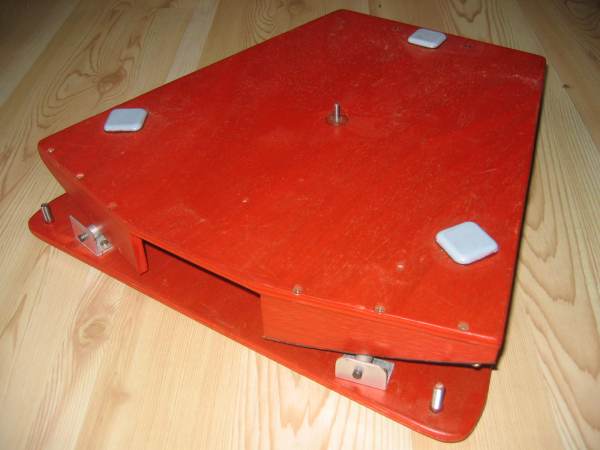
INTRODUCTION
Cet accessoire est une précieuse option que je vous conseille vivement. Elle procure un réel confort d’observation. On dispose ainsi d’un véritable suivi motorisé d’environ 1h20. Une mise en station sommaire ultra-rapide est tout à fait suffisante pour une utilisation en visuel. Si sa conception peut sembler ardue, sa réalisation est des plus basique et son coût dérisoire.
Principes
Concept de base
Les planchettes équatoriales fonctionnent toutes sur le même principe, décri en détail sur de nombreux sites.
Pour résumer, l’axe de rotation horaire étant incliné vers le pôle céleste, nous allons considérer le cône dont la génératrice passe par l’horizontale du lieu d’observation. Il suffit de «découper» ici ou là quelques portions de cette surface conique et de les supporter par quelques galets judicieusement placés pour répondre aux belles lois du principe de l’isostatisme. Ainsi, l’axe horaire est en quelque sorte dématérialisé, on obtient une structure extrêmement compacte, sans porte à faux. Comme pour toute monture équatoriale, il faut pour obtenir un bon fonctionnement, que cet axe de rotation passe par le centre de gravité de l’ensemble mobile, télescope et embase.
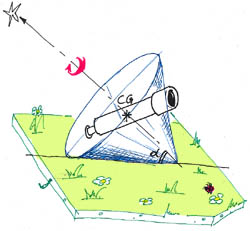
Principe isostatique
Pour immobiliser un objet dans l’espace, il faut et il suffit de « bloquer » 6 degrés de liberté : 3 translations et 3 rotations selon un trièdre de référence Oxyz.
Ainsi un cube se maintient par 3 points sur une face matérialisant un plan, 2 points sur une face adjacente matérialisant une ligne, et 1 point sur une face adjacente aux deux premières matérialisant un point (ou une butée).
Enfin, si un plan se supporte par 3 points, un cylindre (ou un cône) se supporte par 4 points.
Dans notre cas, nous ne voulons conserver qu’un seul degré de liberté, celui correspondant à la rotation autour de l’axe horaire. Il faut donc bloquer 5 degrés de liberté et surtout pas une de plus ! Chaque galet en contact bloquera 1 degré de liberté, une rotule en bloquera 3.
Un système qui présente plus de 6 degrés de liberté bloqués est hyperstatique. Cela se traduit par un système bancal (une table à 4 pieds n’est jamais stable car un plan ne se porte que par 3 points) ou subissant des contraintes, parfois souhaitables, mais préjudiciables dans bien d’autres où l’on cherche la précision de positionnement, ce qui est notre cas ici.
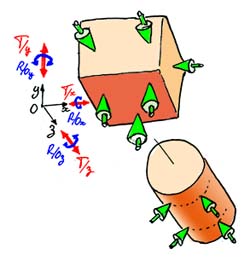
Matérialisation de l’axe de rotation horaire
Plusieurs type de planchettes sont possibles.
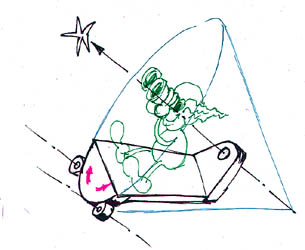
Les plus basiques comprennent une rotule (bloquant 3° de liberté) sur l’axe de rotation au sud et un secteur semi-circulaire reposant sur 2 galets au nord (bloquant 2 de liberté). Si la fabrication est des plus rudimentaire, elles ont le défaut d’un encombrement plus important si on veut (et on doit) respecter que la position du centre de gravite passe par l’axe de rotation.
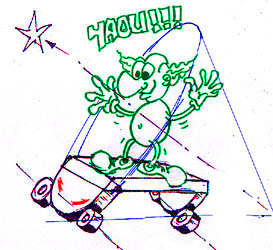
Pour gagner en compacité sur le même principe, il suffit de mettre un deuxième secteur circulaire au sud à la place de la rotule. Les 4 galets bloquent 4 de liberté. Il convient d’ajouter une butée selon l’axe horaire. On positionne ainsi la hauteur de l’axe de rotation à sa guise.
On le voit, ces 2 systèmes utilisent des secteurs lisses semi-circulaires, ce qui est bien pratique pour leur réalisation. Cela impose que les galets d’appui soient parallèles ou perpendiculaires à l’axe de rotation. Cependant, le palier nord et ses galets dépassent de l’ensemble de la structure.
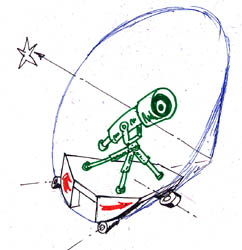
Une belle alternative est de transformer le secteur circulaire nord par 2 petites portions de « coniques » verticales, c’est le VNS (Vertical Nord Sector). Ainsi, les galets porteurs – qui peuvent être motorisés – sont à l’horizontal. Mécaniquement, ça travaille mieux. Si on souhaite faire l’entraînement horaire par les galets, l’implantation de la motorisation est facilitée. Enfin, l’ensemble gagne encore en compacité.
Façons de porter les secteurs par les galets
Il y a 3 façons de reprendre les efforts générés par le poids de l’instrument par les galets de roulement.
1- L’axe des galets peut être parallèle à l’axe de rotation horaire. Le contact se fait sur un secteur semi-cylindrique.
2- L’axe des galets peut être perpendiculaire à l’axe de rotation horaire. Le contact se fait sur un secteur plan. C’est cet unique galet qui fait office de butée.
3- Enfin, l’axe des galets peut avoir une orientation quelconque. Ici, nous choisirons un axe horizontal par rapport au plan du lieu d’observation. Dans ce cas, le contact se fait sur un secteur perpendiculaire au sol dont la forme est une conique, obtenue par la projection du cercle TNBC sur ce plan . On remarque que ce secteur va déraper latéralement sur le galet lors du suivit. Pour diminuer ce ripage au minimum, il conviendra d’orienter ces secteurs et ces galets par rapport au sommet du cône.
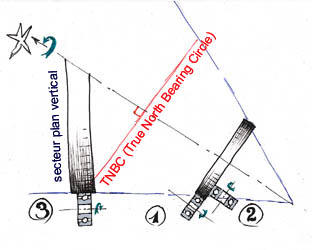
Positions des galets sur les secteurs
Il faut visualiser et tracer les secteurs circulaires (ou les TNBC) en « vraie grandeur », c’est à dire selon l’axe de rotation horaire. La largueur du secteur nord est à déterminer selon l’encombrement de la base du télescope ou son rocker. Pour des raisons de stabilité, on va chercher à écarter à maximum les galets entre eux, tout en considérant la durée du suivi horaire recherchée, dépendant de l’angle alpha.
Pour gagner en compacité de hauteur, on utilisera des galets dont le diamètre ne génère pas un encombrement préjudiciable.
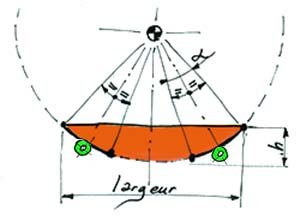
L’entraînement horaire
Deux possibilités s’offrent à nous :
– soit on motorise directement un ou plusieurs des galets porteurs. L’entraînement se fait par simple friction. Il n’y à rien à débrayer en fin de course et à la réinitialisation du système.
– Soit par un entraînement direct sur un autre secteur circulaire, généralement par vis sans fin ou par secteur lisse et écrou « tireur ». Si cette option garantit la transmission, elle oblige un système de débrayage en fin de course.
LES CONCEPTS RETENUS
Généralités
La plate-forme est conçue avec un angle de 45° pour l’axe de rotation horaire et cela pour 2 raisons. D’abord, l’instrument étant destiné à voyager, il doit permettre quelques variations de latitude. Ainsi en région parisienne, il suffit de rehausser les 2 pieds nord pour incliner la plate-forme de 4 ° supplémentaires. En voyage dans le sud de l’Europe, on rehaussera le pied au sud. Ensuite, un angle de 45° est bien plus facile à tracer pour la construction.
La partie mécanique
Pour nos STROCK, j’ai choisi de faire un VNS avec une motorisation par les galets. Cela me semble aller avec le souci de compacité et de rationalisation qui a toujours été de mise lors de la conception de l’instrument optique.
La plate-forme se compose de 2 parties.
– L’embase supérieure sert de socle au télescope. Elle est équipée en face supérieure de son pivot central et des 3 patins de téflon. Sur la face inférieure se trouvent le secteur semi–circulaire sud et les 2 secteurs verticaux nord. Tout le secret de cette machine réside dans ces 3 éléments. Mais qu’on se rassure, le procédé de fabrication est des plus simple, comme nous le verrons plus loin.
– La base inférieure est équipée des galets de roulement. Leurs positions relatives conditionnent un fonctionnement correct de la machine. Un de ces galet est motorisé et transmet le mouvement horaire par simple friction. Un boîtier de piles et une électronique sommaire de commande trouvent leur place ici. 3 pieds réglables en hauteur assurent une bonne assise avec le sol.
Pour respecter les principes isostatiques, nous allons bloquer 5 degrés de liberté, le 6ème resté libre assurera la rotation de l’ensemble. On considère que chaque galets bloque 1 dégré de liberté. Il nous faut donc 5 galets en tout. 1 sera placé sous chaque secteur vertical, 2 répartis sur le champ du secteur semi-circulaire sud et 1 en en butée, sur sa face plane. Leur emplacement permettra un débattement de 20°, conrrespondant à 1h20 de suivi.
La motorisation
J’ai cherché la simplicité maximale. Ici, pas de moteur pas-à-pas ou autre complexité électronique d’asservissement. On utilise un moteur à courant continu associé à une grosse démultiplication par cascade d’engrenages. Le moteur tournant à bon régime, on dispose pleinement de son couple et de sa régularité de mouvement. Un variateur de tension basique permet le réglage fin de l’entraînement.
FABRICATION DE LA PARTIE SUPERIEURE
La planche
Se reporter au plan coté pour le traçage et la découpe de la planche. Bien repérer l’axe longitudinal, l’emplacement du pivot et des 3 patins de téflon qui devront correspondre à la surface de frottement du dessous du rocker.Les 2 secteurs verticaux nord
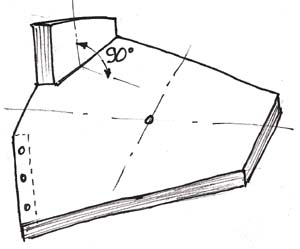
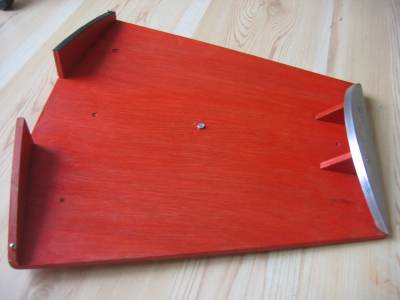
Le secteur semi-circulaire sud
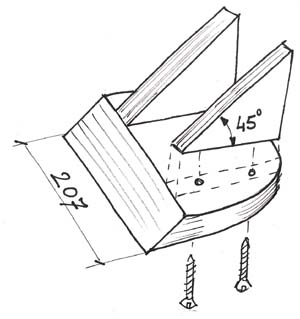
Tracer et découpez ce secteur. Là aussi, la découpe circulaire doit être un peu plus généreuse que la cote finale théorique de 135 mm de rayon. La finition de ce secteur ce fera ultérieuement par ponçage. Scier, raboter ou limer à 45° la corde du secteur afin qu’il s’applique bien sur la planchette. Débiter les 2 goussets en s’appliquant à la réalisation de l’angle à 45°. Coller, visser ces goussets sur le secteur, puis l’ensemble obtenu sur la planchette en vérifiant bien la position par rapport à l’axe longitudinal, la corde doit être perpendiculaire.
Mise en forme des secteurs nord et sud
Pour ce faire, nous allons faire un montage pour matérialiser l’axe de rotation horaire.
Tracer, découper le gabarit du montage. Ici, seul compte le respect des 2 cotes fonctionnelles encadrées.
Visser sur le champ du coté à 45°, 2 gongs de porte démontables.
Visser solidement ce gabarit sur la planchette, bien précisément sur l’axe longitudinal.
Afin d’éviter toute déformation pendant l’usinage et rigidifier cet ensemble, visser un gousset bien d’équerre entre le gabarit et la planchette.
Sur un fort tasseau, visser l’autre partie des 2 gongs.
Comme on le constate, la planchette peut maintenant osciller sur ces 2 gongs, dont l’axe matérialise l’axe de rotation horaire.
Il suffit de fixer et maintenir fermement le tasseau dans la bonne position pour exécuter l’usinage des secteurs.
Pour les 2 secteurs verticaux nord, on fixera le tasseau à 45°. Utiliser des serres joint, les mors d’un établi réglable, des étais, une vieille poutre, bref, tout ce qui garantira une parfaite rigidité à ce tasseau. La base sera visée dans une planche bien horizontale où on aura pris soin de tracer la projection de l’axe de rotation.
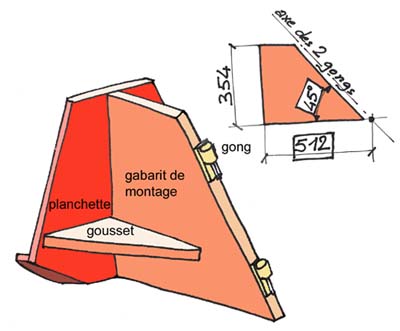
L’usinage
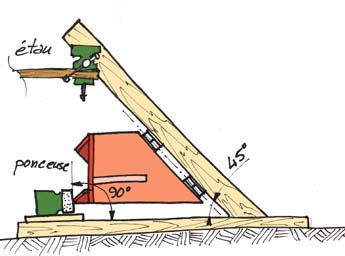
On va poser le coté d’une ponceuse à bande sur une planchette et on va vérifier soigneusement la perpendicularité de la semelle de ponçage. Un simple bridage par appui à la main doit suffire pour tenir la machine bien calée sur sa planchette.
Placer la machine et la planchette sur la planche de base, bien perpendiculaire au tracé de l’axe. Faire osciller le montage pour caler la position de la machine dès qu’elle effleure un point de contact avec l’un des secteurs. Relever la planchette, mettre en route la ponceuse, et amener doucement cet ensemble au contact de la machine pour usiner les secteurs. Après chaque passe, on avance d’un chouya la ponceuse sur la base et on recommence. L’opération est finie quand l’intégralité de la surface des 2 secteurs est parfaitement poncée et que l’on atteind la cote de 10 mm.
Simplissime non ?
ATTENTION : Toujours avoir à l’esprit que tous les usinages, quels qu’ils soient, doivent se faire IMPERATIVEMENT en opposition. C’est à dire que les forces d’usinage doivent s’opposer aux forces d’avance de l’outil. Dans le cas contraire, on s’apercevrait très vite qu’il y a un grave problème… On travaillerait en avalant, la pièce de bois serait littéralement happée par la ponceuse.
Pour le secteur sud, on calera verticalement le tasseau sur la planche de base. Il faudra juste faire attention à caler tout ce montage pour travailler que sur le bord de la ponceuse, afin de ne pas être gêné par la planchette elle-même.
L’usinage se fait de la même façon que précédemment.
Ainsi, grâce à ce montage rudimentaire, nous avons généré 3 belles surfaces parfaitement coaxiales.
NOTA : Le secteur sud peut être usiné avant son montage définitif sur la planchette (cf : même principe que pour les haches du télescope). Dans ce cas, il faudra particulièrement veiller à son bon positionnement.C’est ce qui a été fait ici pour ce proto.
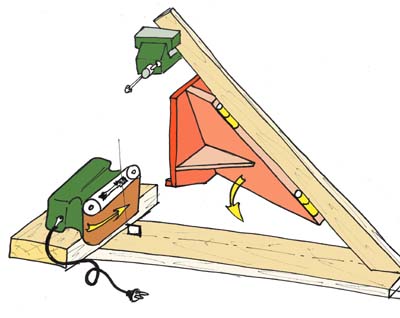
Finitions
Pour solidifier ces surfaces, nous allons les durcir en imprégnant les champs des secteurs de CTP avec de l’Epoxy après les avoir um peu humidifiés avec de l’alcool à brûler. Passer un chiffon légèrement imbibé d’alcool sur la surface encollée pour bien faire pénétrer la résine dans le bois. Recommencer jusqu’à être certain que tous les trous soient comblés.
Une fois bien sec, réutiliser le montage pour une finition très légère du ponçage. C’est de la peau de fesse !
FABRICATION DE LA PARTIE INFERIEURE
La planche
Tracer et découper la planche selon le plan coté. Repérer l’axe longitudinal et les 2 axes des galets des secteurs verticaux nord. Ils doivent converger vers le point matérialisant l’extrémité du cône, en dehors de la planche.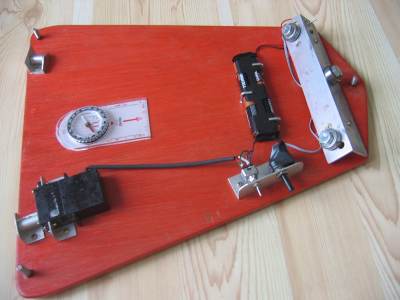
La motorisation
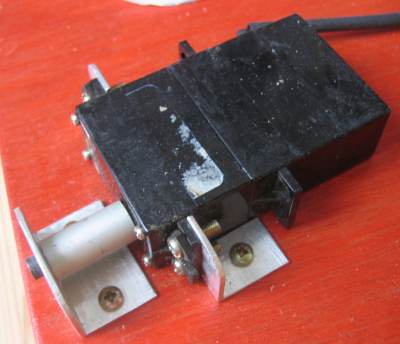
Il nous faut partir de cet élément pour dimensionner les positions respectives des autres composants. La hauteur de l’axe de sortie déterminera la hauteur de l’axe des galets nord, donc la hauteur totale du système en fonction de leur diamètre retenu. L’implantation des galets sud devra assurer l’horizontalité de la planchette supérieure. J’ai choisi d’utiliser un servo-moteur de radio-modélisme pour son faible encombrement, sa tension d’utilisation de l’ordre de 5 V et de sa démultiplication intégrée. Voici la méthode de modification. Il faut ouvrir le servo pour effectuer quelques opérations.
– il faut ôter les 2 butées de débattement qui limitent la rotation de l’axe de sortie avec une micro fraise, une petite lime, un cutter…
– il faut ôter le potentiomètre directement pris sur l’axe de sortie,
– il faut ôter le petit circuit électronique d’asservissement du moteur. Quoiqu’il doit être très intéressant de le conserver car justement, c’est un régulateur ! Mais il faudrait étudier comment on pourrait l’utiliser et le piloter. Une autre fois…
– Souder 2 fils d’alimentation aux bornes du moteur, en conservant les petits condensateurs d’anti-parasitage (c’est mieux) et le passe fil.
On dispose maintenant d’un beau moto-réducteur assez compact, avec un couple de sortie intéressant et assez bien démultiplié. Mais hélas, pas suffisamment…
Les paliers nord
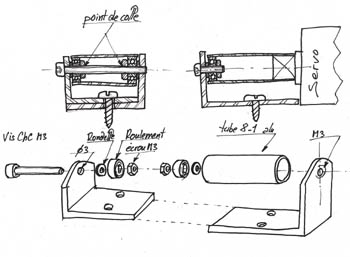
Il faut se procurer 3 petits roulements à billes de 6 à 8 mm de diamètre externe. Une auscultation sérieuse d’une vieille imprimante ou photocopieur est une mine inépuisable de petits composants intéressants, roulements, visserie, connecteurs, interrupteurs…
Ils seront fixés par une vis sur de petites équerres en alu percés et taraudées, tirées d’un cornière en L. La hauteur de l’axe des galets doit être la même que la hauteur de l’axe de sortie du moteur.
Couper 2 bouts de tube en alu qui feront office de galets. Le diamètre intérieur doit correspondre à celui des roulements.
Dans mon cas, j’ai récupéré des roulement de 6 mm, fixés avec des vis M3, emmanchés dans un tube de 8-6 mm.
Un galet sera porté par 2 roulements, fixés sur 2 équerres, l’autre motorisé sera porté par 1 seul roulement d’un coté et par l’axe de sortie motorisé de l’autre.
Complément de démultiplication
Un peu de calcul s’impose ici.
Nous connaissons maintenant 4 données :
– la vitesse sidérale (Vs), ne chipotons pas et prenons 1tr/24h soit 1tr/1440 mn .
– le diamètre (D) légèrement approximatif des 2 secteurs sud (ce sont des coniques…). Il est matérialisé par le trait rouge du schéma du paragraphe « position des galets sur les secteurs ». Certains anglo-saxons appellent ce cercle le TNBC (True North Bearing Circle). Dans notre cas, il mesure 716 mm.
– Le diamètre (d) des paliers nord. Dans mon cas, 8 mm.
– La vitesse de rotation (Vm) de notre moto-réducteur. Il faut chronométrer le temps en seconde nécessaire pour effectuer 10 tours, le moteur étant alimenté par une pile de 4,5 V. Il suffit de diviser 600 par la valeur mesurée pour avoir sa vitesse en tr/mn.
La vitesse de rotation du galet (Vg) est donc dans ce cas :
D /(d x Vs) soit 0,062 tr/mn ou encore 16 mn/tr, à un poil près.
On constate que ce résultat est bien inférieur à la vitesse mesurée de notre moto-réducteur. Il nous faut donc ajouter une démultiplication supplémentaire dont le rapport exact est de Vg/Vm.
Pour ce faire, nous allons utiliser la démultiplication d’un deuxième servo-moteur. Dans mon cas, j’ai conservé l’intégralité de la cascade de pignons pour avoir en sortie un vitesse de l’ordre de 10 mn/tr. La vitesse sera modifié par une légère baisse de la tension, soit :
10 x 4,5 / 16 = 2,8 V. Mon moteur travaille encore dans une plage correcte de fonctionnement. On aurait pu envisager de diminuer le diamètre du galet.
Il faut retourner à nos travaux de chirurgie et disséquer un deuxième servo :
– on ne conserve que les éléments supérieurs du boîtier correspondant à la démultiplication.
– On récupère le pignon de sortie du moteur.
– Comme pour la première intervention, on ôte les 2 butées de débattement et le potentiomètre.
On possède entre les mains un joli réducteur qui a le bonheur de s’adapter parfaitement sur notre moto-réducteur.
On assure la transmission mécanique entre ces 2 éléments comme suit :
– Manchonner à force un axe (tige en laiton ou corde à piano) dans le pignon récupéré sur le 2ème servo. Une petite soudure ou un collage peut être nécessaire.
– Manchonner à force cet axe équipé du pignon sur l’axe de sortie du premier moto-réducteur. Cette opération est grandement facilité par la présence d’un trou taraudé en son milieu, prévu initialement pour la fixation des guignols de commande du servo. Un collage peut s’avérer nécessaire. Bien régler la hauteur du pignon pour qu’il s’engrène bien.
– Se débrouiller d’une façon ou d’un autre pour assurer le guidage de cet axe au niveau du boîtier de démultiplication. J’ai prolongé un peu cet axe pour qu’il vienne se loger dans le trou d’un palier existant.
– Raccorder les 2 éléments, moto-réducteur et démultiplication en utilisant les grandes vis d’assemblages existantes et quelques points de colle cyano.
Il suffit de manchonner à force le galet sur l’axe de sortie.
La motorisation est finie et peut être installée sur la planchette. Le couple est énorme, le moteur ne calera pas !
NOTA : on voit que sur le même principe, on aurait pu attaquer le bloc de démultiplication à un autre étage de la cascade d’engrenage et modifier en conséquence le rapport de réduction. Il suffisait de manchonner à force l’axe de liaison métallique directement sur le pignon de son choix en perçant et faisant déboucher le trou de son palier du boîtier en plastique. Dans ce cas, les 2 éléments ne seraient pas alignés entre eux, mais ça n’aurait aucune conséquence fâcheuse.
Fixation des paliers nord et de la motorisation
Les 2 galets doivent avoir une longueur suffisante pour permettre le glissement des secteurs verticaux lors de la rotation. Ils sont positionnés au centre des secteurs pour utiliser l’intégralité du débattement disponible. La motorisation est placée à champ sur la planche inférieure. Ainsi, elle est bien protégée. Je l’ai fixée par 2 petites équerres en alu. J’aurai pu aussi la coller directement sur la planchette inférieure avec du scotch double face. Il faut juste s’assurer de la bonne orientation de l’axe des galets et du moto-réducteur vers le sommet virtuel du cône de référence.
Les paliers sud
3 roulements à billes sont ici aussi nécessaires. J’ai choisi des roulements de roller, très largement surdimensionnés dans notre cas. Mais à cet emplacement nous n’avons pas de contrainte de dimension… Ils sont directement fixés par des vis dans une cornière en aluminium. Deux planches de bois à 90° auraient très bien fait l’affaire. La position des 2 galets latéraux doit permettre d’une part une bonne horizontalité de la planchette supérieure, d’autre part un débattement de +/- 10° pour assurer 1h20 de suivi. Le 3ème galet est fixé au centre de la cornière et joue le rôle de butée axiale. On fera dépasser son diamètre extérieur de 1 mm du flan de la cornière pour assurer le jeu de fonctionnement du secteur semi-circulaire sud. La cornière est rigidifiée, fixée et collée sur la planchette inférieure grâce à 2 goussets. S’appliquer à respecter l’angle de 45° pour un parfait contact des galets sur le secteur lisse. Respecter le bon positionnement de cette ensemble sur la planchette inférieure, centrage et équerrage par rapport à l’axe longitudinal. Vérifier que les 2 secteurs verticaux reposent bien au centre des galets quand la planchette supérieure est est en place et bien à l’horizontale. Notre système est opérationnel ! C’est avec un certain plaisir qu’on posera les planchettes l’une sur l’autre, qu’on constatera et appréciera la qualité du mouvement. On remarquera avec plaisir qu’on ne s’est pas ruiné dans cette opération et que ça n’a pas pris trop de temps à faire. Pour être pleinement fonctionnel, il nous reste quelques menus travaux de finition.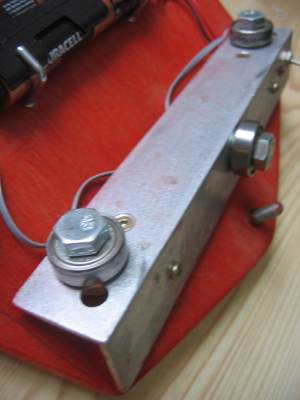
L’électronique
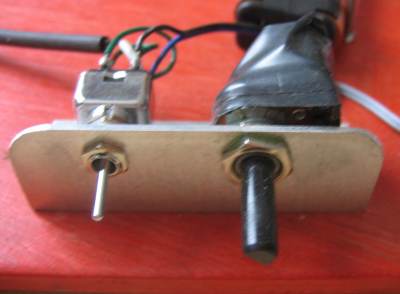
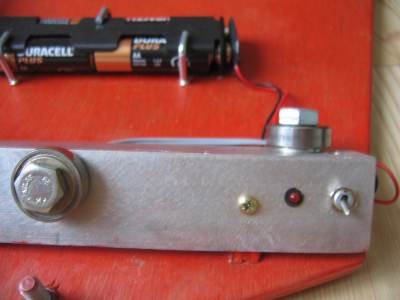
Les finitions
– On constate que le système d’entraînement est tributaire de la qualité de l’adhérence du galet moteur sur le secteur lisse. Pour augmenter le « grip », j’ai collé à la néoprène une bande de caoutchouc récupérée sur une chambre à air de vélo. D’autres solutions sont possibles. A voir aussi au niveau du galet d’entraînement, en utilisant ceux d’une d’imprimante par exemple…
– Il est confortable de mettre 2 butées de débattement en fin de course pour éviter les déraillements intempestifs. Ca peut être 2 petites vis ou n’importe quoi fixé à 2 extrémités de son choix des secteurs lisses.
– Coller 3 patins de téflon sur la planchette supérieure et matérialiser l’axe de rotation vertical du télescope par une vis M4 (idem que pour le socle du télescope).
– Mettre 3 inserts filetés M8 sous la planchette inférieure dans lesquels on placera des vis qui feront office de pieds réglables.
– Pour faciliter la mise en station, je vous conseille vivement de coller une boussole sur la planchette inférieure (scotch double face) en l’orientant précisément sur l’axe longitudinal.
Il ne reste plus qu’a passer du verni, de la peinture ou de la lasure sur votre œuvre pour aller l’étrenner !
UTILISATION
La mise en station
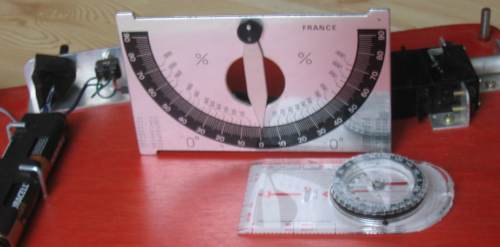
Pour du visuel, ne nous prenons pas le choux. On cherche juste à garder l’objet dans le champ de l’oculaire un gros paquet de minutes.
La boussole intégrée va permettre un alignement sur le méridien ultra rapide. Si la précision vous gagne, coller à coté l’angle de dérivation magnétique du jour.
Pour assurer une bonne assise sur le sol un peu mou d’un pré, mettez quelques cales en bois sous les 3 pieds. Pour le réglage de l’inclinaison en fonction de la latitude du lieu d’observation, j’utilise un clinomètre.
Ces deux réglages fait, vous n’avez plus qu’à poser le télescope dessus, caler le système sur sa butée à l’est, mettre en route le moteur et observer dans le plus parfait des conforts. Le potentiomètre permettra d’affiner et d’ajuster précisément la vitesse de rotation.
Vous pourrez toujours affiner la mise en station par la célèbrissime méthode de Bigourdan si le besoin s’en fait sentir (s’écrire le petit protocole qui va bien).