Les outils
Les premiers travaux de fabrication consistent à réaliser les outils nécessaires. Les premiers outils sont les disques de doucissage, de polissage, de parabolisation et de retouche. Il faut ensuite fabriquer la machine à polir et l’appareil de Foucault.
L'outil de 156 et les proportions du plâtre
14 novembre 2008 : Connaissant le nombre et les caractéristiques des outils à réaliser, il est aisé de calculer le volume du plâtre fini. Mais pour acheter le plâtre et pour préparer les gâchées, il faut aussi connaître la densité du mélange eau plâtre et les proportions en masse des deux composants.
Or le vendeur n’a pas su nous dire le nombre de kilogrammes nécessaires pour réaliser nos 19 litres d’outils. Et les encyclopédies donnent le plâtre à densité 2,8… Oups ! Ça va être plus lourd que le verre ! Il faut donc faire des mesures des proportions.
Il est d’autant moins inutile de faire un essai que, faute de compétence préalable, cela permet d’appréhender la difficulté du gâchage et la rapidité de prise.
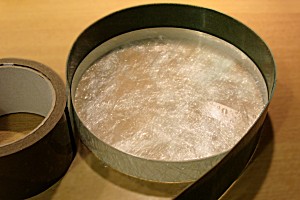
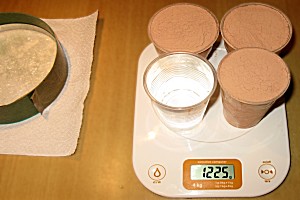
On utilise un miroir de télescope de 150 mm de diamètre (Il est non aluminé car il est en cours de polissage). Non pas que ce soit nécessaire, on aurait pu faire un simple cylindre de plâtre. Mais cela est plus proche de ce qu’il faudra faire pour mouler les grands outils dans le bloc de Suprax. Tout particulièrement pour le glissement de l’outil dans le creux du bloc lors du démoulage.
Le miroir est huilé, puis protégé par trois feuilles de film alimentaire. La surface est savonnée pour permettre le démoulage. Un bord en carton est scotché autour. Le tout est posé sur une planche. Cela permet de taper par en dessous pour faire décoller les bulles d’air qui, sinon, resteraient accrochées entre le film alimentaire et le plâtre.
On sait seulement qu’il faut saupoudrer 3 volumes de plâtres dans un volume d’eau. On utilise des gobelets de plastic de machine à café qui ne pèsent rien… Une mesure d’eau (225 cc) pour trois mesures de plâtre (675 cc). Cela fait 990 grammes de plâtre. Soit 81% de plâtre en masse dans le mélange initial. Voilà une donnée importante : 81% en masse.
Le mélange se fait bien. Ce plâtre ne se met pas en tas difficiles à mélanger. Il faut le brasser une première fois et le laisser reposer une minute. Cela fait ressortir les zones trop chargées en eau. On peut alors le mélanger à nouveau pour bien l’uniformiser.
Au passage un enseignement intéressant : La hauteur du moule était de 25 mm. On n’a pas pu le remplir complètement pour éviter les débordements. Et cela se tasse un peu en vibrant les bulles. Donc 10% de marge sur la hauteur des moules semble nécessaire.
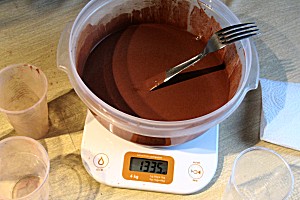
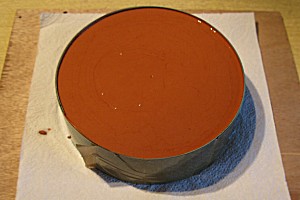
Il n’est pas difficile de retirer le carton scotché. Mais le moule adhère au film qui adhère au verre. Il est impossible de séparer les deux blocs. De plus cela ne glisse pas à cause du chanfrein du miroir. Le plâtre est descendu dans le petit chanfrein de 1 mm qui brode le miroir. On le savait, et là on se rend bien compte que même pour un petit miroir il faut rompre le chanfrein de plâtre pour faire glisser l’outil.
On obtient un bel outil moulé sur le miroir. Il y a juste l’empreinte des quelques bulles d’airs qui étaient coincées dans les trois couches de film. Un beau disque de plâtre de 21,5 à 22,5 mm d’épaisseur et de 156 mm de diamètre. Soit un volume de 432 cc.
Une fois pris et avant ébavurage et séchage, le moulage pèse 837 g. Il est donc de densité 1,95. Revoilà une donnée importante : Densité 1,95 avant séchage. C’est moins lourd que le verre finalement.
On ne s’attendait pas à cette densité. Il est donc resté du plâtre de la gâchée. Avec le surplus, on a rempli un cul de bouteille qui pourra servir d’outil de 80 mm.
Après avoir taillé des chanfreins pour ne pas s’abîmer les mains et rectifié le dos, il ne pèse plus que 810 g. Et il reste à le faire sécher.
Donc pour faire 18,9 litres de moulage (Deux 600, un 300 et un 150 à 25mm au bord), qui feront 37 kg, il faut 30 kg de plâtre.
Comme on en a acheté 50 kg, il y en a de trop. Mais bon, il eut fallut savoir les proportions et seulement ensuite acheter 25 kg en gros et pas cher d’un coté puis dans une autre boutique les 5 à 8 kg au détail et deux fois plus cher. On va pouvoir revendre du plâtre.
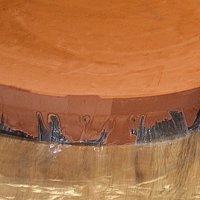
Les outils de 600 mm
22h20 : On a vérifié que la table est bien de niveau. Elle est protégée par un film plastique. Le miroir est enduit de graisse siliconée pour faciliter le démoulage.
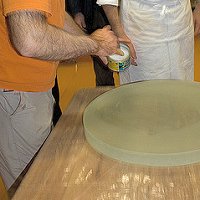
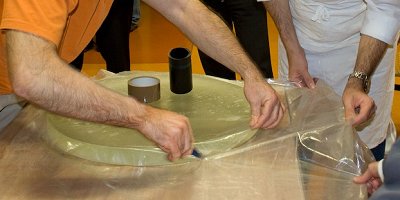
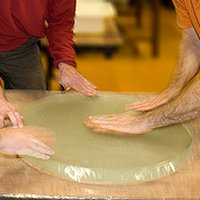
On découpe un morceau de film plastique à la taille du verre plus six centimètres de rabats. Il faut le lisser pour retirer les bulles d’air. Le film va permettre le démoulage.
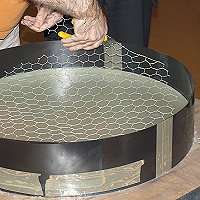
On entoure le miroir avec une bande constituée de vieilles radiographies découpées et scotchées bout à bout. Il faut bien serrer pour éviter au plâtre de filer dans les plis du film entre le verre et la bande.
On a armé le plâtre avec un grillage de clapier à lapins. Car les grands outils (de plus de 400 mm) peuvent s’écailler –voir éclater– lorsqu’on ébouillante la poix ou lorsqu’on les manipule un peu vivement au doucissage.
On s’est décidé pour faire des outils de 30 mm au bord. C’est a priori trop épais : 20 mm suffisent pour des 600 ! Mais pour un usage en collectivité… Le dosage du plâtre et de l’eau est à réaliser avec soin : 15,36 kg de plâtre pour 3,49 kg d’eau. Ils seront très lourds.
Lors du dosage, il ne faut pas tasser le plâtre pour éviter qu’il ne fasse des grumeaux. Il faut aussi être très au calme pour doser sans se tromper… N’est-ce pas ?
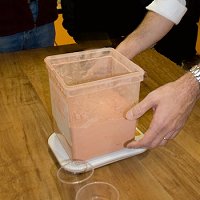
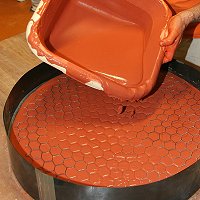
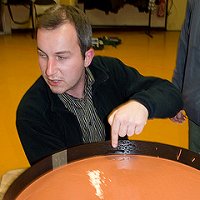
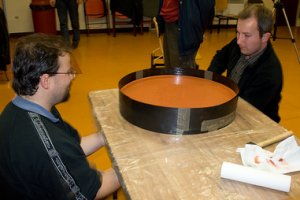
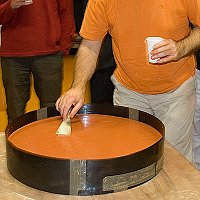
22h34 : On verse en deux fois, mais presque dans la foulée, car on incorpore le grillage (mouillé) au milieu. Avec la couleur de la pâte, certains on envie de goûter le chocolat… Mais c’est le moment de frapper par en dessous de la table pour que les bulles d’air se décollent et remontent à la surface. Ces chocs font remonter le grillage qu’il faut repousser au milieu de la pâte. Avec les 30 mm d’épaisseur, il n’est pas trop difficile de mettre le grillage à peu près au milieu du plâtre. On s’y est mis à trois à la manœuvre pour frapper les bulles. Hardie ! Pendant ce temps il faut que quelqu’un d’autre nettoie à grande eau les ustensiles.
22h40 : Enfin on a le temps de souffler. C’est le moment de prendre un verre pour fêter l’arrivée du bloc de verre : Signe tangible du début des opérations lourdes de notre ambitieux projet.
22h46 : Lorsque le plâtre commence à prendre, sa surface vire au mat. C’est le moment de ferrer le plâtre : Armé d’une spatule, on lisse sa surface pour crever et combler les bulles qui affleurent ; et pour parfaire le niveau du moulage.
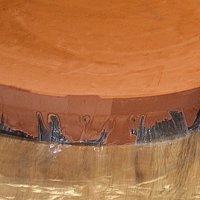
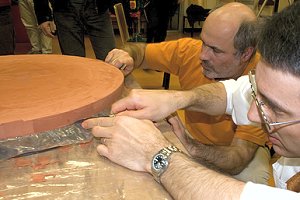
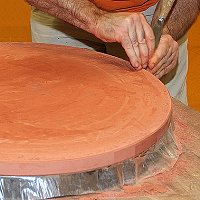
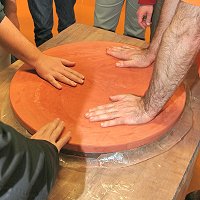
22h53 : La bande latérale se décolle sans difficulté dès que le plâtre est plus dur. Il y a quelques coulées qui cassent facilement. Il faut alors passer un outil pour couper ou gratter le plâtre qui est moulé dans le chanfrein du miroir. Cela facilite le démoulage de l’outil et du verre. Ainsi l’angle de l’outil est moins fragile. Il faut faire cela tant que le plâtre est encore un peu mou. Ce grattage endommage le film qui se retrouve plus ou moins découpé au ras du verre. On ne pourra plus l’utiliser pour manœuvrer l’outil au démoulage.
Il faut aussi tailler un gros chanfrein sur le dos de l’outil pour ménager les doigts des futurs doucisseurs. Pendant ce temps, la réaction chimique s’opère, le plâtre chauffe.
On avait décidé de laisser le plâtre en place sur le miroir une bonne heure pour être certain qu’il ne se déforme pas au démoulage. Pendant ce temps, on nettoie et on prépare les doses pour le deuxième outil de 600 mm.
23h18 : Le démoulage s’est étonnamment bien passé comparativement à celui de l’outil de 150 mm. La graisse silicone, chauffée par la réaction du plâtre, n’adhère pas du tout. C’est comme si les quelques bulles d’air, dilatées par l’échauffement aidaient au décollage de l’outil. On arrive par une traction maintenue à faire pénétrer de l’air entre le verre et le film. L’outil se soulève un soupçon puis on peut le faire glisser et l’attraper par ses bords pour le retirer. La feuille de plastique reste collée sur l’outil pendant cette opération, mais elle se retire sans difficulté en tirant dessus. Il reste bien quelques marques de plis sur l’outil. On estime que cela n’est pas important.
23h20 : On attaque le deuxième outil…
Les outils de la troisième reprise
Février Mars 2011 : Troisième reprise au doucissage et polissage
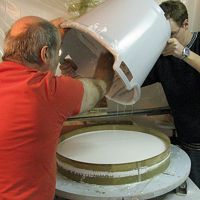
Cette fois-ci, le Staturoc est blanc et on n’y met pas de grillage. Car pour les premiers outils, il y a une petite possibilité que ce soit le grillage qui ait provoqué la modification du rayon de courbure des outils. Même si nous pensons que c’est plus probablement le séchage qui a été trop court.
La recette est la suivante: Miroir horizontal huilé à l’huile de tournesol, film alimentaire sur l’huile en deux couches croisées. Radiographies pulmonaires cerclées et bien serrées tout autour. Préparation du plâtre avec les proportions exactes. Et il ne faut pas se tromper entre volume et masse dans les proportions… Utilisation d’eau glacée pour ralentir la prise et avoir le temps de bien pétrir pour retirer les grumeaux.
On verse rapidement, on frappe fort et on vibre énergiquement pour faire monter les bulles et on surveille la prise. Il faut que ce soit bien liquide pour que la surface soit bien plate, d’où l’eau glacée et une certaine fébrilité des opérateurs. Quand la prise est faite, on décercle et on racle les chanfreins avec un outil métallique bien d’équerre. Il ne faut pas attendre trop car le plâtre est ensuite très difficile à travailler. Au besoin on rabotte les bosses résiduelles du dos de l’outil. Il est indispensable de bien tailler le chanfrein entre verre et outil, car il gênera fortement le démoulage s’il reste emplâtré…
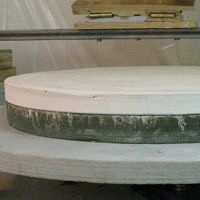
Ce coup-ci on laisser l’outil sécher sur le miroir une semaine avant de démouler. On assure ainsi que le rayon de courbure ne change pas comme sur les outil précédents. Le démoulage est assez vigoureux car on a beau huiler et filmer… ca colle encore.
On réalise deux outils de 600 mm et d’environ 30 mm au bord. Seul inconvénient de cette technique: c’est vraiment très lourd à manipuler.
Les moules à poix
Les expériences un peu laborieuses, des uns et des autres en matière de moulage des carrés de poix de polissage, nous poussent à réaliser un moule à poix en silicone. C’est ce type matériaux qui constitue les moules souples pour la pâtisserie. Par exemple les moules à madeleines ou à cannelés. Ce genre de moules donne de très beaux résultats avec la poix. Ils sont très pratiques car les carrés n’adhèrent pas du tout. Et ces moules sont réutilisables, contrairement aux moules en papier.
Un premier calcul indique qu’il faut environs trois litres de résine pour faire un moule de 72 à 100 carrés de 50x50x10 mm. C’est ce qui définit l’achat de 5 kg de silicone RTV avec 250 g de catalyseur.
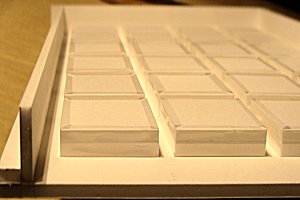
On réalise l’empreinte du moule avec du carton plume. C’est la disponibilité du carton plume en feuille de 50×65 cm sur 5 mm qui a finalement fixé la taille de l’empreinte et donc des moules. On va réaliser une empreinte de 6×4 carrés de 50×50 mm.
Il faudra réaliser trois moules pour produire 72 carrés d’un coup et il faudra espacer ces carrés de 12 mm sur l’outil pour couvrir toute la surface de nos grands outils.
Le moule est fait en premier. Sur la photo, le moule n’est pas fermé sur un côté pour mieux montrer l’alignement des carrés. Chacun est constitué de deux carrés de carton fixés ensemble par un scotche replié sur les faces. Le fond du carton est abondamment noyé de colle blanche (celle qui est utilisée en reliure d’art…) puis les carrées sont posés et pressés. Ainsi, ils collent au fond et la colle fait un bourrelet en périphérie des carrés qui empêchera la résine de passer sous les carrés. Car cette résine est faite pour mouler les plus infimes détails de l’empreinte. Si elle passe sous les carrés, on risque l’arrachage lors du démoulage. Or il faut que l’empreinte soit réutilisable pour trois moules. Détail supplémentaire, il faut chasser les plis du scotch aux coins des carrés pour que la résine n’y rentre pas.
Comme on ne connaît pas la densité de la résine et que l’on doute des vitesses de prise indiquée sur le pot, on fait un essai. Avec des chutes de carton plume, on réalise 16 carrés de 25×25 mm. Même technique du scotch et de la colle. Ceux-ci sont collés sur une simple feuille de papier. Le tout est entouré d’un mur de Lego, lui aussi collé sur la feuille à la colle blanche et tapissé avec des bouts de papier collant.
On coule 300 grammes de résine additionnée de 10 grammes de catalyseur. Un petit tube de médicament est bien utile pour doser le catalyseur. Attention : c’est un produit toxique. On découvre à cette occasion la viscosité de la résine. C’est très visqueux, mais ça ne colle pas. C’est assez peu usuel ! La résine coule du pot en faisant une grosse boule, mais une fois le pot relevé, les bavures n’en finissent pas de couler en fin film. Il faut une cuiller pour y mettre rapidement fin et pour compléter le dosage. Le mélange avec le catalyseur –très liquide– est un peu lent à faire à la cuiller.
Le mélange est donc dosé à 3%. Selon les dires du pot, cela doit prendre en 15 heures à température ambiante. Au bout de 8 heures, dont certaines sur un radiateur, on démoule. Le dos est bien un peu collant aux doigts.
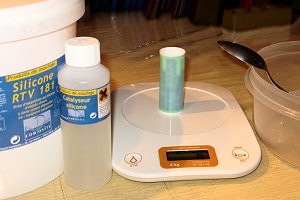
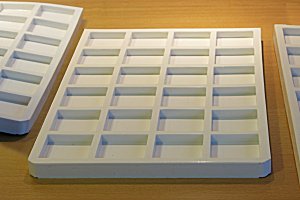
Cela donne un moule de 17 mm d’épaisseur : Parfait. Cela permet de dire que la densité résultante est de 1,09 pour préparer les quantités pour les grands moules. En fait les grands moules seront mesurés à une densité de 1,18… sans doute les imperfections des mesures et la présence de petites bulles dans la résine du fait du brassage du catalyseur.
Les grands moules sont dosés à 1000 grammes de résine plus 40 ou 45 grammes de catalyseur. Ils sont bien pris au bout de huit heures. Ils ne sont pas mis sur radiateur, car le moule se banane très fortement. Il reste donc sous une planche avec 12 kg sur la tête.
Pour faciliter le démoulage, on a mis de petites chutes de carton dans les angles. Ces chutes permettent de soulever les angles et ainsi d’avoir une première prise pour démouler.
Ces moules présentent un seul désagrément : Ils empestent pendant des heures.
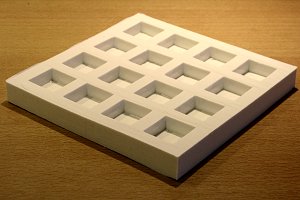
Le moulage de la poix pour la troisième reprise
12 décembre 2008 : Le dos étant rectifié, il faut maintenant garnir un disque de plâtre avec des carrés de grès pour constituer l’outil de doucissage.
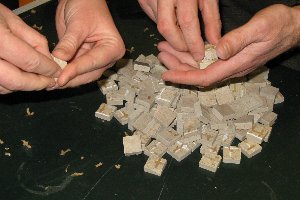
On n’a pas trouvé de carrés de grès bien grands au magazin du coin : Ils ne font que 25 mm de coté. Ils sont collés sur un maillage de papier, bien trop proches les uns des autres. Cela risque de nous empêcher de bien nettoyer les abrasifs entre les carrés. Il faut donc séparer les carrés à la mains. Sans quoi nous les aurions directement posés dans la poix.
On colle à la poix. Avec une vielle poix de récupération provenant de tous les copains qui ont fait des miroirs au club.
On peut aussi coller avec de la colle époxy. Mais on pense que le plâtre peut présenter des variations de forme qui pourraient être génantes pour les abrasifs les plus fins. Peut-être qu’avec la poix on pourra contrecarrer cela par un pressage.
Ceux qui n’ont pas taillé de miroir découvrent les joies de la poix. Ça colle partout, ça éclate sous les coups mais ça s’enfonce sous les ongles, c’est difficile à nettoyer et ça brûle quand on y met les doigts.
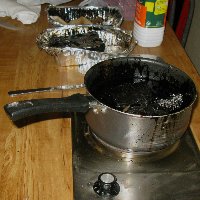
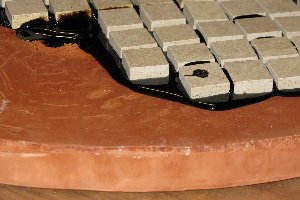
On coule la poix avec la casserole et on se dépèche de poser les carrés de grès. On essaye d’espacer les carrés régulièrement. Et on réchauffe avec de grands coups de chalumeau avant de recouler de la poix.
Le chauffage au chalumeau est assez spectaculaire. La poix doit projeter des produits qui s’enflamment en pétillant. C’est le feu d’artifice.
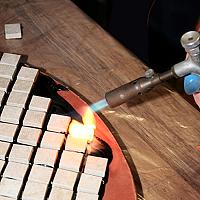
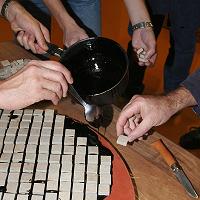
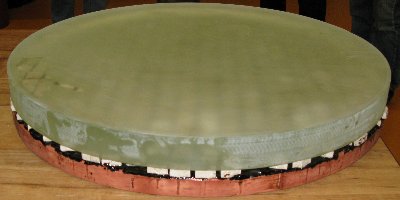
19 décembre 2008 : On a ajouté quelques carrés sur les bords : De petits carrés coupés à la grignotteuse avec quelques louches de poix et de petits coups de chalumeaux. Puis on a posé le miroir dessus pour égaliser la hauteur des carrés.
Le miroir et l’outil étant resté toute la semaine dans un sous-sol non chauffé, la poix est dure. On l’a chauffée avec deux ou trois bouilloirs d’eau chaude. On s’est un peu assis dessus pour aider. Et puis on a laissé ça toute la semaine à presser.
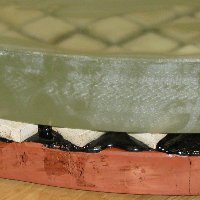
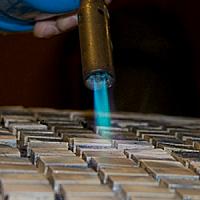
2 janvier 2009 : Mais ça n’a pas été suffisant et nombreux sont les carreaux qui dépassent. Nous avons alors employé la manière forte et l’usage du chalumeau pour ramollir la poix localement et enfoncer les récalcitrants.
Même ainsi et après la première séance de doucissage, de nombreux carreaux ne sont toujours pas en contact, notamment au centre de l’outil. Nous décidons un pressage après avoir sensiblement tiédi la surface de l’outil au chalumeau et en le laissant une semaine dans le local qui a été isolé de ses bouches d’aération et dont le convecteur électrique a été mis en marche.
Après une semaine de pressage de plus, la surface de l’outil reste irrégulière. Les carrés de céramique ne sont pas à plat sur le verre. Nous décidons de revenir au carbo 80 pour réunir l’outil sur le miroir. C’est un peu le monde à l’envers… Normalement on commence au carbo 80 pour mettre le verre en forme, là c’est l’outil qu’il nous faut mettre en forme.
On passera donc une soirée au carbo 80 pour que presque tous les carrés de céramique finissent par toucher le verre. Il nous semble que la poix ne flue pas assez sous les carrés pour qu’ils se mettent de niveau. À ce moment, on imagine qu’il eu mieux vallu coller les carrés avec une mince couche de colle époxy.
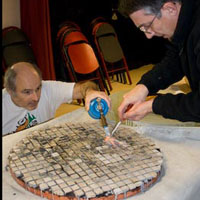
Ce n’est qu’un mois plus tard (voir au 6 mars) en essuyant des déconvenus lors du pressage de l’outil de polissage que l’on découvre que les deux outils sont bi-convexes. Alors que nous les avons moulés sur le verre en creux de 8 mm, ils présentent sur leurs deux faces un bombé de 4 mm… Les outils ont donc travaillés durand le séchage. Sans doute que nous les avons retirés du verre trop vite et qu’ils se sont affaissés sur le carton qui les supportaient pour la fin du séchage…
L'outil de doucissage de la troisième reprise
11 mars 2011 : Fabrication de l’outil avec des carrés de verre
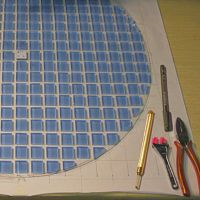
Cette fois-ci, on cherche à éviter que l’outil ne soit trop agressif vis-à-vis du verre pour limiter le risque de devoir revenir à des abrasif très gros et pour éviter le risque de grosses écailles lorsque l’on pose l’outil sur le verre. On utilise donc des carrés de pate de verre comme il s’en vend pour la déco des salles de bain. C’est une matière moins dure que le grés céramique.
Ces carrés sont vendus encollés sur une résille. Là on les a décollés, nettoyés et recollés sur un filme plastique afin de les positionner d’un seul coup sur l’outil enduit d’araldite. Travail inutil et qui nous a conduit en plus à espacer plus fortement les carrés, ce qui gêne le travail en dispersant l’abrasif… Il faut garder les carrés sur la résille et encoller la résille. On a aussi découpé des demi et quart de carrés ce qui est inutile et réduit les emplacements où l’on peut glisser les doigts pour prendre l’outil. Il est bien plus important de pouvoir mettre les doigts sans se couper et placer l’outil délicatement sur le miroir sans risque de chocs. Le seul intérêt d’avoir espacé les carrés est de faciliter le travail de nettoyage. Intérêt assez moyen, car de toute manière c’est long à faire.
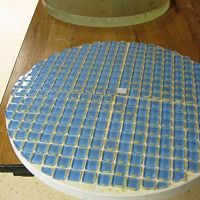
Les carrés ont été collé à l’araldite sur l’outil préalablement enduit d’une couche d’imperméabilisant pour béton. Précaution inutile voir dangereuse! L’imperméabilisant sur du Staturoc est inutile. L’imperméabilisant est parfois moins adhérant au Staturoc que l’araldite et s’est décollé sur au moins un carré.
L’outil a ensuite séché au dessus du miroir afin que les carrés desendent au contact du verre. Précaution inutile voir dangereuse. L’araldite n’a pas bien entouré la base de tous les carrés car elle a coulé vers le bas elle aussi. On a créé des poches de rétention d’abrasif à la base des carrés sous des ponts d’araldite qu’il a fallut cassés. Ce qui a fragilisé certains carrés et provoqué des éclatements, donc des écailles de carrés, donc des rayures sur le miroir.
Mais on est globalement plus content de cet outil. Il a bien gardé sa forme de permettra un quatrième retour au doucissage. Mais on n’espère pas…
La machine à polir
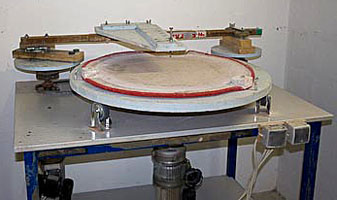
L’opportunité de l’achat de la machine de Jean-Marc Lecleire nous a fait gagner un précieux temps de cogitation, de fabrication pour un coût pas forcément différent qu’une construction intégrale par nos soins. De taille imposante, nous l’avons démonté pour faciliter son transport et à l’occasion, nous nous sommes copieusement barbouillés les vêtements avec les moteurs qui pissaient l’huile dès lors qu’on les inclinait. Son remontage s’est fort bien déroulé et nous l’avons placé installé dans un recoin des locaux de la MJC. Il nous faudra méticuleusement veiller à la température et la propreté de ce local.
27 février : Après démontage, tranpsort et remontage, un boîtier électrique de moteur a été endommagé. Réparation du boîtier électrique et remontage. Mise en place d’un dais de plastique pour protéger la machine des poussières volantes et des courrants d’air. On enduit l’outil de plâtre de 600 mm de trois couches d’apprêt d’étanchéité. On est ainsi plus assuré de ne pas déposer de poudre de plâtre sur le miroir en cours de travail.
6 et 13 mars : Purge de l’huile des réducteurs. Quasiment rien ne sort… Injection de 140 ml d’huile SHELL DONAX TA dans chaque réducteur. C’est une huile que l’on trouve pour les boites de vitesses automatiques et les directions assistées, en vente dans les magazins de trucs de bagnole. Notre outil est trop épais et ramponne dans son bras de manoeuvre. On réhausse le bras en ajoutant des cales de bois sur les axes. On en profite pour nettoyer le bras : Ponçage et couche de Rustol (espèce d’anti rouille aussi utilisée pour imprégner et durcir le bois).
Les améliorations de la machine pour la troisième reprise
Décembre à juin 2011: On profite de la rupture de la machine et des travaux de doucissage pour l’améliorer.
On a placé un excentrique sur le moteur du bras afin de pouvoir régler progressivement et comme on le souhaite ce débattement. On a placé un excentrique sur le bras porte outil pour pouvoir régler finement le débord de l’outil. On a éloigné un peu les trois axes pour permettre la rotation des excentriques. Ces excentriques sont faits avec du contreplaqué et une grande tige filetée. On réalise un charriot véhiculé par la tiges et qui est guidé dans une cuvette rectangulaire.
On a renforcé par des plaques d’acier la planche de la table qui pliait sans cesse sous l’effort des puissants moteurs. On a monté la table sur des roulettes pour la manipuler plus facilement dans notre petit réduit de travail.
On a mis une charnière sur le bras porte outil. On n’a donc plus à faire des efforts inconsidérés sur le bras pour le soulever et changer les outils. C’est peut-être une explication de la rupture…
On a changé de tapis pour un tapis de sol de camping plus facilement lavable. Le précédent se chargeait de produit à polir et devenait rigide au bord tout en restant mou au centre… Enfin on a changé les butées du miroir pour qu’elles ne bougent plus, qu’elles n’appuient pas sur le tapis, qu’elles poussent vers le milieu du verre et qu’elles ne présentent aucune partie métallique saillante. Il resterait à prévoir un outillage pour décoller le miroir afin de pouvoir y glisser les doigts dessous.
Et on s’est bien juré de nettoyer souvent la machine pour ne pas travailler dans la crasse…
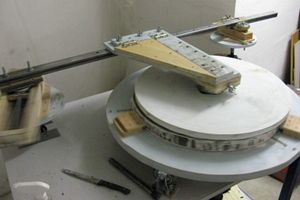
Le tapis molleton de la troisième reprise
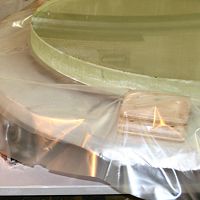
Nous n’étions pas très content de notre tapis à poils sous le miroir. Une sorte de tapis de sol rond à bas prix. Certes, Jean-Marc Lecleire utilisait ce type de tapis. Mais le nôtre avait épongé les coulures de produit à polir si bien qu’il était devenu rigide en périphérie. De plus il fallait le visser sur le plateau pour qu’il ne fasse pas des plis lorsque l’on tournait le miroir.
Pour le troisième doucissage, nous avons repris le dos du miroir qui n’était pas assez plat à notre gout. Nous en avons profité pour virer le vieux tapis encrouté et pour passer à un tapis de sol de gymnastique. Il fait juste 5 à 6 mm d’épaisseur. Il est plus facile à laver que le tapis à poils mais il n’a pas le même comportement. Car chacun sait qu’un tapis se forme sous les objets qui lui sont posés dessus. Tandis qu’un platique est purement élastique. Il va donc forcer sur les bosses et ne pas porter les creux. Un rapide calcul d’écrasement permet de voir que ce type de tapis s’enfonce de moins d’un dizième de millimètre sous la pression du verre et de l’outil. Le moindre creux au dos du verre est donc mal supporté.
Notre insatisfaction sur le tapis est remonté d’un cran lorsque le maître opticien David Vernet nous a expliqué qu’il restait sur les conseils de Texereau: trois couches de couverture de laine espacées de deux feuilles de papier fort type kraft. Une sorte de moleton d’environ 15 mm d’épaisseur. Mi septembre 2011 nous avons donc mis quatre couches de couverture de laine très usagée avec trois papiers kraft et le tout protégé par des feuilles plastiques pour ne pas risque de remplir de produit à polir.
Le moleton constitué fait bien 15 mm et dépasse de chaque coté du verre de 10 mm. La partie qui dépasse se loge dans un creux des cales latérales, ce qui évite les plis. Un platique de protection est posé au dessus et est vissés sous les cales avec du jeu pour ne pas écraser le moleton. Enfin une grade feuille de plastique récupère les coulures et permet de soulever le miroir pour le tourner ou passer les doigts dessous.
Les outils de polissage
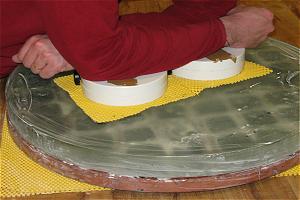
20 février 2009 : La poix a été fondue et moulée, puis collée au chalumeau sur le deuxième disque en plâtre de 600 mm de diamètre. Dommage qu’on ai un peu radiné la fonte ( 1 kg au lieu des 2 kg prévus). Mais il se faisait tard et c’est très long à fondre… Il manque donc quelques carreaux, tronqués sur la périphérie. Pour remédier à cela, on va laisser fluer la poix lors des pressages pour combler ces trous, faire que ça devienne des rectangles à la place des carrés et ça devrait aller. Donc la semaine prochaine : pressage, rognage (attention, ça saute partout, à faire dans la cuvette d’eau pour minimiser), prévoir une bouilloire d’eau, des baches ou des nappes papier pour protéger, et ensuite, collage des bandes de mousse au chalumeau.
27 février 2009 : Nous avons chauffé la poix et le miroir avec de l’eau chaude du robinet et d’une bouilloire. Ce n’est pas facile quand on n’a pas une cuvette assez grande pour contenir l’outil à plat… Et en plus nous avons fait une écaille. L’eau de la bouilloire a créé des tentions thermiques dans le plâtre froid. Nous coulons de la poix sur les arrêtes de l’écaille pour éviter les poudres abrasives.
Nous avons pressé l’outil sur les carrés de poix avec un mélange gras d’oxyde de zirconium et d’eau. C’est ce qui est utilisé pour polir. Là, c’est pour éviter que la poix ne colle sur le verre. Ce n’est pas encore pour polir. Le résultat n’est pas tip-top Ça ne presse pas au centre ! On fera avec, vu que le centre sera travaillé par la parabolisation.
Ensuite on rogne les carrés pour ne pas qu’ils se collent les uns aux autres. Tout le monde a observé avec amusement les éclats de poix qui volent quand on tape dessus. Et surtout le miroir qui colle dans la poix dès qu’il y a trop de poids et plus de poudre blanche. Les carrés du bord sont ra-plat-plats et collés les uns aux autres. On devra recreuser ces sillons au fer à souder la semaine prochaine.
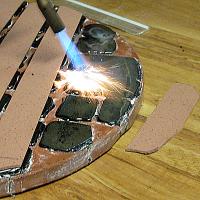
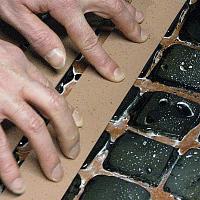
6 mars 2009 : On a oublié le fer à souder pour recreuser des sillons… On colle donc les bandes de polyuréthanne sur les carrés de poix. Et on pose l’outil sur le miroir pour presser. Comme la feuille de polyuréthanne a été stockée roulée, elle n’est pas bien à plat. Il faudra deux semaines pour qu’elle se moule bien à plat sur le miroir.
Et là… surprise ! En cherchant à comprendre pourquoi la poix est plus mince sur les carrés du bord qu’au centre, on découvre que l’outil de plâtre est biconvexe de 4 mm. Alors qu’on l’a moulé sur le miroir avec un creux de 8 et un dos plat… C’est sans doute que nous n’avons pas attendu assez que le plâtre sèche !
L’outil reste sur le miroir pendant la semaine. Il reste donc en forme et est prêt à polir dès que l’on arrive le vendredi. On ajoute juste un peu d’eau au vaporisateur, on accroche l’outil sur le bras moteur et on met en marche. En cours de soirée, il faut remettre un peu d’eau toute les 30 minutes environ. On a vérifié que l’outil ne se déforme pas pendant la semaine : La poix ne flue presque pas sous le polyuréthanne… Surprenant ! Le local est un sous-sol non chauffé, sa température doit être entre 10 et 18 dégrés.
3 avril 2009 : Après 12 heures de polissage, on fait le premier contrôle à l’appareil de Foucault. On a le fer à souder. On en profite pour refaire quelques sillons entre certains carrés de poix. On rogne un peu les autres au couteau. Le centre de l’outil ne touche toujours pas sur le verre. Décidément, la poix ne flue pas beaucoup.
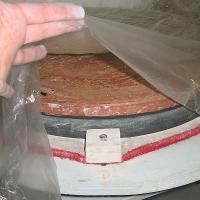
L'outil de polissage de la troisième reprise
Juillet 2011 : Fabrication de l’outil et de la piscine de trempette
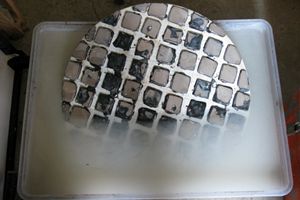
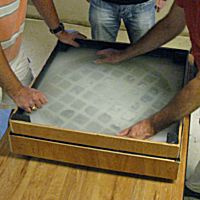
Anciennement pour presser l’outil de poix sur le miroir, nous faisions ainsi: L’outil, dans une grande bassine pas assez grande, était aspergé d’eau très chaude puis posé sur le miroir à température ambiante. Ca donnait l’impression de marcher, mais on se faisait un peu peur avec la température de la poix.
Là on cherche la petite bête pour la troisième reprise et on a des doutes sur la qualité du pressage comme sur l’homogénéité de température lors du travail. Donc on décide de fabriquer une piscine pour la trempette. C’est fait avec quelques planches, du vernis et du joint de baignoire.
L’outil est posé au fond sur des cales pour que l’eau puisse lui chauffer le dos. On enduit de blanc et on pose le miroir dessus. On verse ensuite de l’eau jusqu’au dessus du miroir pour bien chauffer le dos aussi.
On tourne de temps en temps le miroir au dessus de l’outil ce qui fait circuler l’eau et assure que l’on n’est pas en train de coller.
L’outil pour le polissage après le troisième doucis est fait avec un certain manque de poix: Seulement un kilo… On a donc étirer les carrés qui se trouvent espacés de 6,5 à 7 cm au lieu des 6 cm règlementaires.
On n’a pas retenu de reprendre le polyuréthane pour polir plus vite. On va essayer de voir au plus tôt l’apparition d’un astigmatisme, et on va essayer des courses de polissage tant qu’il y a du gris et que l’on peu voir où le verre s’use. On expérimente avant la parabolisation, … bref on va y aller plus doucement.
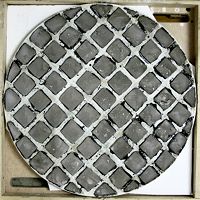
L'outil de parabolisation de la troisième reprise
21 septembre 2011 : Fabrication de l’outil avec des carrés poix. 24 septembre: Premier polissage-pressage.
Le nettoyage des vieux outils couverts de vieux carrés de poix usagées est un travail salissant, long et pénible. Nous avons essayé sur un 300 et un 400 de passer la poix au chalumeau et de la râcler. Cela marche bien, c’est rapide et peu salissant mais gare au feu. Il faut être à trois et chauffer avec parcimonie, car le coup de chaud sur le 300 en Staturoc l’a fait casser… on l’a recollé à l’Araldite ! Le 400 en plâtre, pourtant plus mince, a tenu.
Sur l’outil de 600, pas question de risquer de casser, on a rippé les carrés à la spatule et au marteau comme pour un rognage. Mais comme ils ne voulaient pas venir il a fallut râcler ce qui a fait une montagne de poudre collante. Pourtant les autres outils n’avaient pas présenté cette difficulté… Et on hésite toujours à râcler fortement tant le risque d’attaquer le plâtre et de faire des poudres agressives inquiète. La finition au White Spirit a été tout aussi pénible vu les masses de poix refusant de se laisser râcler. Mais on pense que le dernier débarbouillage de la poix doit bien laisser un film de poix protecteur.
Sur certains outils, on avait passé un produit d’imperméabilisation pour béton. Précaution a priori inutile pour le Staturoc qui est un plâtre étanche. Mais finalement c’est une mauvaise idée. Ce produit fait une bouillie lors du nettoyage au White Spirit. On ne sait pas si les carrés de poix suivants vont bien coller la dessus…
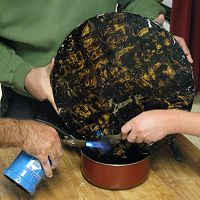
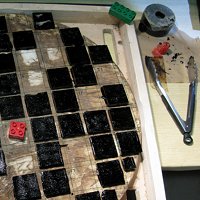
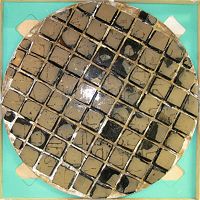
Le collage des carrés fraichement sortis du moule silicone est un travail surtout long. Aidé d’une pince, on chauffe les carrés au dessus d’une bougie jusqu’à ce que la poix coule et on presse rapidement pour que cela adhère bien. On avait des carrés bien refroidis depuis plusieurs jours et un outil forcément froid vu sa taille. Il faut donc bien chauffer la poix pour que ça colle.
Cette fois-ci, pas de pressage à l’eau chaude. On barbouille d’oxyde de zirconium bien épais (une dose de poudre pour à peine une dose d’eau) et on polis. Après un peu plus de deux heures de travail, la poix a chauffé par le frottement et le pressage a commencé. Il faut même faire un premier rognage car des carrés se touchent déjà.
L'appareil de Foucault
Plusieurs copains ont déjà un appareil de Foucault. Ils ont été fait sur les principes énoncés par Texereau (voir dessin à droite) avec source
La source lumineuse et le couteau sont solidaires et mobiles sur une platine X/Y. La source lumineuse se réfléchit sur un miroir à 45° pour permettre de serrer les faisceaux aller et retour. Il semble qu’il est indispensable d’avoir une fente et un couteau solidaire pour les grands miroirs très ouvert (un calcul d’optique assez simple permet de s’en convaincre). Mais à défaut d’avoir calculé les aberrations pour des faisceaux très écartés, ceux-ci seront resserrés au maximum… lumineuse fixe et couteau mobile. Mais il nous en faut un qui soit digne de ce miroir ambitieux.
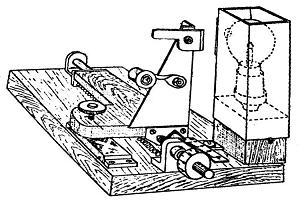
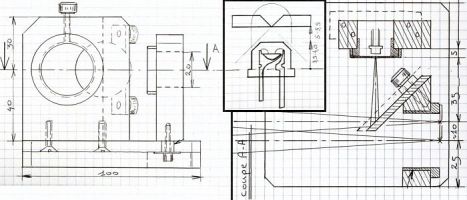
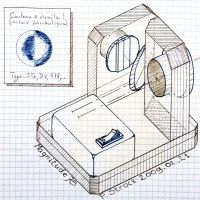
Techniquement, compte tenu des matériaux disponibles dans nos chutes, il est réalisé en plexiglas transparent de 15 mm, acier inox pour les vis, laiton pour les radiateurs, diode de haute luminosité et miroir doré…
Le tout est monté sur deux tables micrométriques à verniers précis à 10 µm. C’est Didier qui nous prête ses tables pour la durée du travail.
Pour l’implantation des différents éléments, en considérant que l’œil directeur est le droit, donc que le nez est à gauche, on est obligé de mettre le miroir et la source lumineuse à droite pour avoir une meilleure ergonomie. Comme le miroir est utilement placé derrière le couteau pour dégager la vue, la fente doit être à droite. Le truc avec un couteau solidaire de la fente, c’est de tout mettre du même coté. Cela dégage un coté pour voir où est le retour de l’image quand on cherche la position pour installer le Foucault. Sinon ça empêche de voir ou bien ça empêche de serrer les faisceaux…
Cette puissante réflexion découle aussi de l’analyse du Foucault de Jean-Marc Lecleire qui a le couteau à gauche avec la fente à gauche. Ce qui donne des reliefs inversés sur les figures… par rapport au sens usuel d’interprétation des reliefs par le cerveau. Cela oblige aussi à écraser le nez sur l’appareil pour la mesures des zones très externes des grands miroirs. Pour la frime, Guillaume nous a récupéré dans les surplus un beau petit miroir doré du plus bel effet. Nous ferons donc des images dorées avec notre Foucault.
Parmi les fonctionnalités, nous souhaitons pouvoir pratiquer le test de l’étoile artificielle. Indispensable pour contrôler l’astigmatisme facilement. Donc il faut pouvoir remplacer la fente par un trou et le couteau par un oculaire. Cela tombe bien, car Guillaume nous a aussi récupéré au surplus un trou calibré de 10 µm. Juste ce qu’il faut pour le rayon de la tache de diffraction au centre de courbure qui est de 6 µm sur notre miroir.
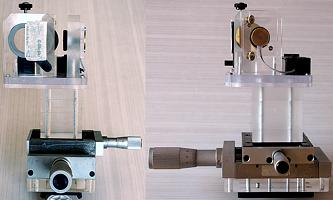
Il faut plusieurs semaines pour fabriquer ce bel appareil. Mais quel allure ! Les filletages sont visibles dans le plexiglas, tout est transparent… très tendance, quoi !
Pour ne pas avoir le menton dans la vis micrométrique on rehausse le bazar sur un cube de plexiglas. Et pour le fixer, on l’équipe d’une plaque de raccord rapide de pied photo. On utilisera le pied photo de nos jumelles 20×80. À l’usage, c’est parfaitement bien calé et ne bouge pas lors des manœuvres des vis micrométriques.
Le couteau (lame de rasoir provisoire sur la photo de gauche) sera amovible car fixé sur un raccord de plomberie de 32 mm. On peut ainsi le remplacer par un oculaire de 31,75 pour observer l’image de diffraction du trou. Avec d’autres raccords de plomberie on peut a loisir refaire un support pour un fil ou pour une lame de phase…
Sur la photo de droite, le trou de 10 µm a été retiré. On peut ainsi observer la diode blanche de 1800 lumens environ (équivalente à une lampe de 30 W à elle toute seule parait-il). Elle est montée sur une tige laiton et une pièce de 10 centimes pour dissiper la chaleur. Ce sont les piles qui sont un peu faibles pour une telle puissance.
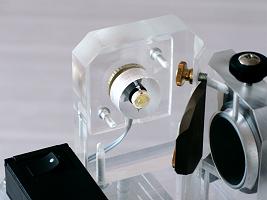
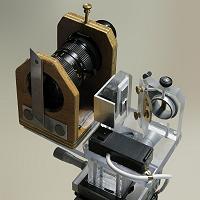
À l’été 2009, les difficultés de mesures au Foucault sont clairement soupçonnées. C’est plus précisément la reproductibilité des mesures qui est en cause sur un masque de Couder à 10 zones. Les plus petites zones ne font que 18 mm de large, et il faut en apprécier le gris simultanément sur le diamètre du miroir à 5 m de distance.
On a donc réfléchit au Foucault automatique dont un bel exemplaire est développé par Alexandre Becoulet au sein de la SAF, à la Sorbonne. Pour ne pas se compliquer trop vite avec la motorisation requise, Christian commence par nous faire un montage de caméra sur objectif avec une diode, une fente et un couteau intégré.
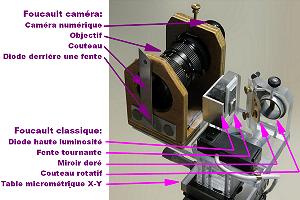
C’est super simple. Il faut juste arriver à bien plaquer le couteau sur l’objectif.
On lit l’image par une ligne USB sur un PC portable. Et l’on est très heureusement surpris de constater deux choses: Premièrement la stabilité de l’image permet de juger plus facilement de l’équivalence de gris entre zone droite et gauche du masque; il n’y a plus de difficulté de placement de l’oeil ni de contorsion du cerveau pour juger de deux points gris forts distant. Deuxièmement les niveaux de gris numérisés sont bien plus distinct que les gris analysés par le cerveau. Il en découle une grande facilitée de mesure. C’est plus distinct, plus rapide et plus reproductible. De plus, la lecture peut être collégiale ce qui est pédagogique mais aussi plus sujet à pinaillage et donc plus précis encore. En tout cas, pour nos mesures en cours de travail nous le préférons.
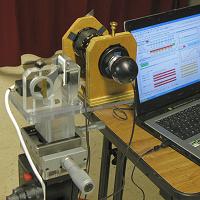
Le poste de mesure est donc composé de la table micrométrique avec au dessus le Foucault classique et le Foucault caméra. Le classique est toujours utilisé pour juger de l’astigmatisme avec un trou de 10 µm et un occulaire de 10 mm.
À coté de ça on trouve obligatoirement un PC avec le visualiseur vidéo et le fichier Excel de calcul.